Because the Brinell hardness tester can measure a wide range of hardness values of the sample, it is used in the measurement of Brinell hardness values of unquenched steel, cast iron, non-ferrous metals and soft bearing alloys in production.
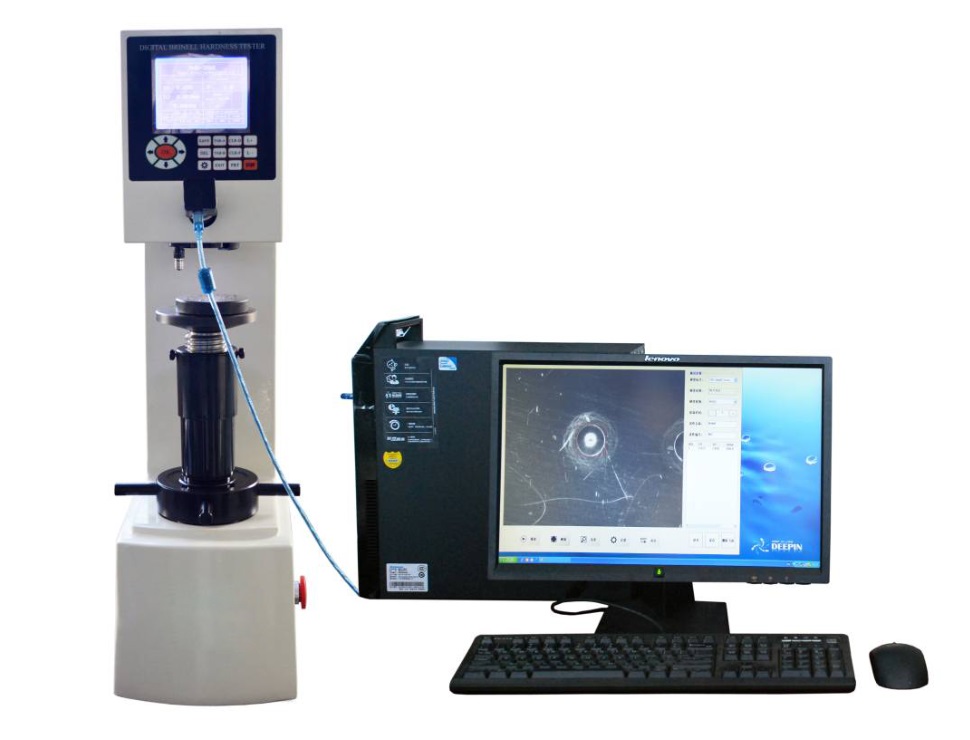
Taking the automatic Brinell hardness testing machine LHB3000A as an example, let’s talk about some common faults and methods.
- The load error exceeds ±1.0% or is unstable. Causes and troubleshooting methods for this failure:
(1) The force point blade is loose, the force point blade should be adjusted and tightened;
(2) The wear of the force point blade and fulcrum will increase the load error to varying degrees, and the blade should be repaired;
(3) The position of the adjustment block on the load lever is not appropriate. It can be moved forward or backward according to the situation. Adjust it properly and fix it tightly;
(4) The compression spring is corroded, which increases the friction with the pressure shaft and main shaft bushing. The rusted parts should be cleaned and applied with protective oil or replaced.
(5) The loading is not stable and there is impact and vibration. Factors causing instability should be eliminated.
- The loading speed cannot be controlled within the specified time. If the loading speed is too fast or too slow, the main reason is that the viscosity of the reducer oil is too small or too high. The reducer should be cleaned and the reducer oil should be replaced.
- The measured hardness value is inconsistent with the indication value of the standard hardness block. Causes and troubleshooting methods for this failure:
(1) The Brinell hardness tester is not installed horizontally, and the Brinell hardness tester should be adjusted to a level level;
(2) If the surface of the steel ball is not smooth or the diameter exceeds the tolerance, use a micrometer to select a qualified steel ball and replace it;
(3) The error of the indentation measuring device is too large, and the allowable error of the indentation measuring device should be adjusted to ≤±0.5%;
(4) The weight cannot be placed vertically. The weight will rub against the back cover of the hardness tester. You should check whether the lifting ring is hung on the key blade and whether the hanger boom is straight. Otherwise, the lifting ring should be hung on the key blade and the crane should be straightened. hanger;
(5) The perpendicularity between the spindle and the test bench platform, and the coaxiality difference between the spindle axis and the lifting screw axis should be analyzed and adjusted according to the situation.
- The Brinell hardness tester is repeatedly loaded and unloaded. Causes and troubleshooting methods for this failure:
(1) The push rod of the push button switch is too long, and the A and B contacts of the steering switch cannot be disconnected from the A1 and B1 contacts. The length of the push rod should be adjusted and fixed;
(2) The installation position of the reversing switch is improper. The movable baffle cannot touch the pin on the reversing switch, causing the reversing switch to not reverse. The installation position of the reversing switch should be adjusted.
- The Brinell hardness tester stops when the load is increased. The cause of this failure is that the contact point of the reversing switch is burned or ablated, resulting in poor contact. The contact point should be cleaned and polished or a new reversing switch should be replaced.
- When the key switch is pressed, the hardness tester does not move, but there is a buzzing current sound. The cause of this fault is the lack of phase in the motor. You should check whether the power supply is normal, whether the power plug is plugged in properly, whether there is an open circuit in the cable, and whether the power switch is intact. , whether the motor wiring is firmly connected, whether a group of motor coils is burned out, and whether the reversing switch contacts are in good contact, etc., should be ruled out separately according to the situation.