Die metallographische Analyse ist eines der wichtigsten Mittel der experimentellen Erforschung metallischer Werkstoffe. Mithilfe quantitativer metallografischer Prinzipien wird die dreidimensionale räumliche Morphologie der Legierungsstruktur bestimmt, indem die metallografische Mikrostruktur zweidimensionaler metallografischer Proben oder dünner Filme gemessen und berechnet wird, wodurch eine quantitative Beziehung zwischen Legierungszusammensetzung, Struktur und Eigenschaften hergestellt wird. Der Einsatz von Bildverarbeitungssystemen bei der metallografischen Analyse bietet die Vorteile einer hohen Genauigkeit und einer hohen Geschwindigkeit, was die Arbeitseffizienz erheblich verbessern kann.
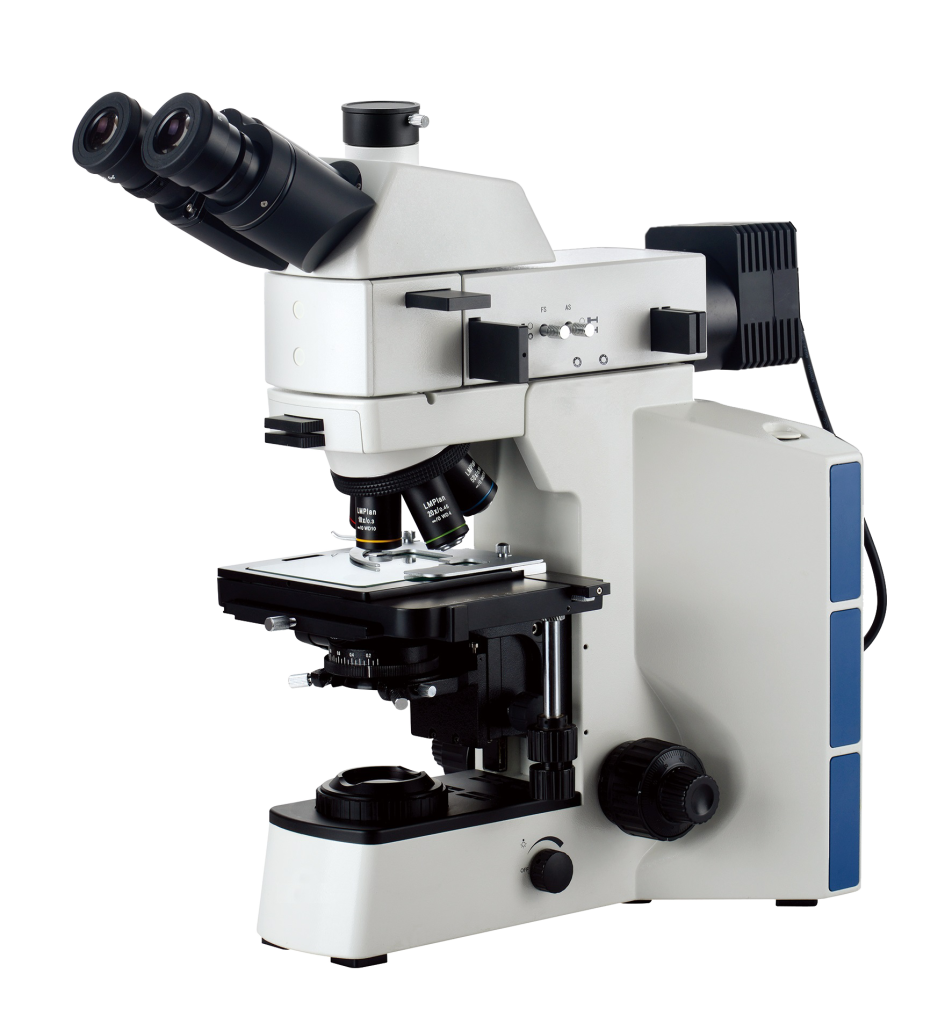
Die quantitative metallografische Computeranalyse entwickelt sich nach und nach zu einem leistungsstarken Werkzeug zur Analyse und Untersuchung verschiedener Materialien, zur Ermittlung quantitativer Beziehungen zwischen der Mikrostruktur und verschiedenen Eigenschaften von Materialien sowie zur Untersuchung der Kinetik der Materialstrukturumwandlung.
Durch die Verwendung eines Computerbildanalysesystems können verschiedene Parameter wie Flächenprozentsatz, durchschnittliche Größe, durchschnittlicher Abstand, Seitenverhältnis usw. von Merkmalsobjekten bequem gemessen werden. Basierend auf diesen Parametern können die dreidimensionale räumliche Form, Menge, Größe und Verteilung von Merkmalsobjekten bestimmt und eine interne Beziehung zur mechanischen Leistung von Materialien hergestellt werden, wodurch zuverlässige Daten für eine wissenschaftlichere Bewertung und rationellere Verwendung bereitgestellt werden Materialien.
Zu den wichtigsten Testelementen gehören:
- Schweißmetallografische Inspektion;
- Metallographische Untersuchung von Gusseisen;
- Qualitätsprüfung der Wärmebehandlung;
- Mikroskopische Inspektion und Bewertung verschiedener Metallprodukte und Rohstoffe;
- Inspektion von Fehlern mit geringer Vergrößerung in Gusseisen, Stahlguss, Nichteisenmetallen und Rohmaterialien;
- Messung der Metallhärte (HV, HRC, HB, HL) und Einstufung der Korngröße;
- Bestimmung des Gehalts an nichtmetallischen Einschlüssen;
- Bestimmung der Tiefe der Entkohlungs-/Karburierungs-Härtungsschicht usw.
Allgemeine Testverfahren:
Schritt 1: Bestimmen Sie den Ort der Probenauswahl und die Probenahmemethode
Wählen Sie den Probenahmeort und die Inspektionsoberfläche unter Berücksichtigung der Eigenschaften und der Verarbeitungstechnologie der Probe aus. Der ausgewählte Ort muss repräsentativ sein.
Schritt 2: Einlegen.
Wenn die Größe der Probe zu klein oder ihre Form unregelmäßig ist, muss sie eingebettet oder festgeklemmt werden.
Schritt 3: Grobes Mahlen der Probe.
Der Zweck des Grobschleifens besteht darin, die Probe zu glätten und in eine geeignete Form zu schleifen. Allgemeine Stahlmaterialien werden oft mit einer Schleifmaschine grob geschliffen, während weichere Materialien mit einer Feile geglättet werden können.
Schritt 4: Feinmahlung der Probe.
Der Zweck des Präzisionsschleifens besteht darin, tiefere Kratzer zu beseitigen, die beim Grobschleifen entstanden sind, und das Polieren vorzubereiten. Für allgemeine Materialschleifmethoden gibt es zwei Arten: manuelles Schleifen und mechanisches Schleifen.
Schritt 5: Probepolieren.
Der Zweck des Polierens besteht darin, die durch das Polieren entstandenen feinen Kratzer zu entfernen und eine glänzende und spurlose Spiegeloberfläche zu erzeugen. Es wird im Allgemeinen in drei Arten unterteilt: mechanisches Polieren, chemisches Polieren und elektrolytisches Polieren, wobei das mechanische Polieren am häufigsten verwendet wird.
Schritt 6: Korrosion der Probe.
Um die Mikrostruktur polierter Proben unter einem Mikroskop zu beobachten, muss eine metallografische Korrosion durchgeführt werden. Es gibt viele Korrosionsmethoden, darunter chemische Korrosion, elektrolytische Korrosion und Korrosion mit konstantem Potenzial, wobei chemische Korrosion am häufigsten angewendet wird.