Universal Testing Machines (UTMs) are essential tools in material testing, allowing engineers and researchers to evaluate the mechanical properties of materials under various conditions. Among the different types of UTMs, the Electro-Hydraulic Servo Universal Testing Machine and the Electronic Universal Testing Machine are two popular options. While both serve the same fundamental purpose, they utilize different mechanisms and technologies that lead to distinct advantages and applications.
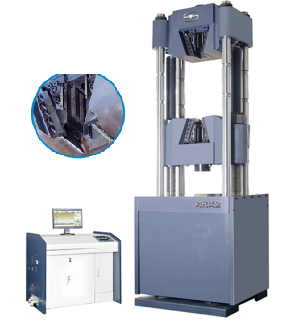
Working Principle
Electro-Hydraulic Servo Universal Testing Machine
The Electro-Hydraulic Servo Universal Testing Machine operates on the principle of hydraulic power. It uses hydraulic actuators to apply force to the specimen being tested. The system is controlled by an electro-hydraulic servo system that precisely regulates the hydraulic pressure and flow. This allows for high force capacities and a wide range of test speeds, making it suitable for testing materials that require significant load application, such as metals and composites.
Electronic Universal Testing Machine
In contrast, the Electronic Universal Testing Machine relies on electric motors and load cells to perform tests. The machine applies force through a screw-driven mechanism, where an electric motor rotates a lead screw to move the testing grips apart or together. Load cells measure the force applied to the specimen, providing real-time feedback to the control system. This type of machine is known for its simplicity and ease of use, making it ideal for testing materials like plastics and textiles.
Key Differences
1. Force Application Method
The most significant difference lies in their force application methods. The Electro-Hydraulic Servo UTM uses hydraulic pressure to generate force, which allows it to handle larger specimens and higher loads. On the other hand, the Electronic UTM uses mechanical means (screw-driven) to apply force, making it more suitable for smaller-scale testing.
2. Speed and Precision
Electro-Hydraulic Servo UTMs generally offer superior speed and precision in force application. The servo system allows for dynamic testing, where the force can be varied rapidly during the test. This capability is crucial for materials that exhibit viscoelastic behavior. Meanwhile, Electronic UTMs provide good precision for static tests, but their speed is typically limited compared to their hydraulic counterparts.
3. Complexity and Maintenance
Electro-Hydraulic Servo UTMs are generally more complex due to their hydraulic components. This complexity can lead to higher maintenance requirements and costs. In contrast, Electronic UTMs are simpler in design and require less maintenance, making them more user-friendly and cost-effective for laboratories with limited resources.
4. Application Range
The choice between these two machines often depends on the specific applications. Electro-Hydraulic Servo UTMs are ideal for high-load tests and materials that require high precision under varying conditions. They are commonly used in aerospace, automotive, and heavy engineering sectors. Conversely, Electronic UTMs are better suited for routine testing of smaller specimens, such as in quality control processes for plastics, textiles, and other lightweight materials.
Both the Electro-Hydraulic Servo Universal Testing Machine and the Electronic Universal Testing Machine have their unique strengths and weaknesses. The choice between the two depends on the specific needs of the testing application, including the type of material being tested, the required load capacity, and the precision needed for the measurements. Understanding these differences is crucial for engineers and researchers to select the most appropriate testing equipment for their material characterization needs.