Aunque el probador de dureza Rockwell tiene una estructura simple y es fácil de operar, si se opera incorrectamente durante mucho tiempo y la prueba de dureza es inexacta, la calidad del producto se verá muy afectada y traerá consecuencias adversas.
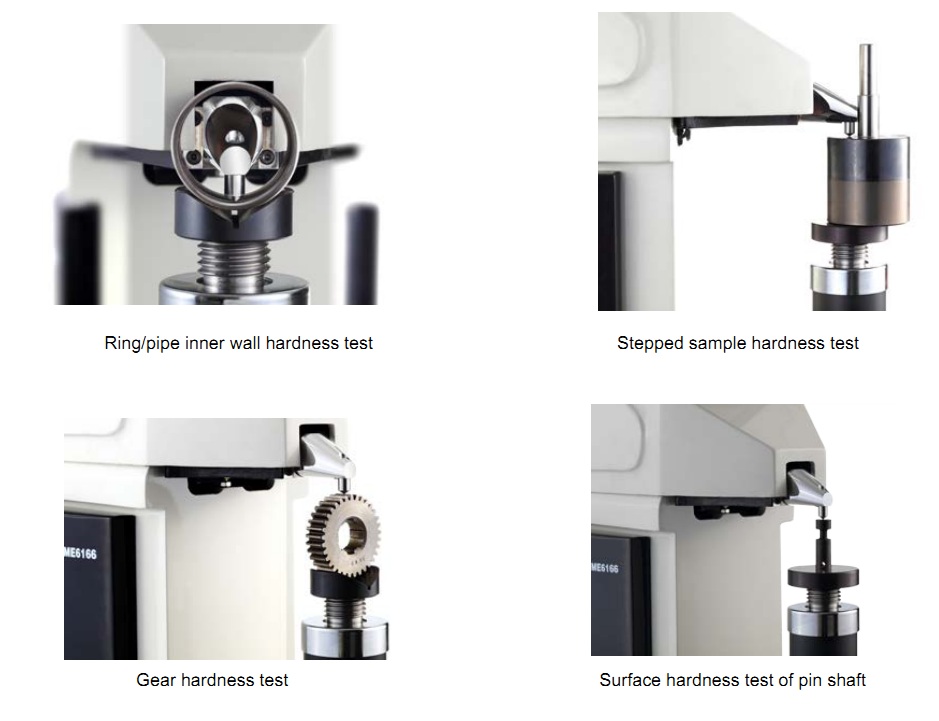
Ahora introduciremos varios errores comunes y sus métodos de tratamiento en la calibración de la siguiente manera:
- Error humano.
(1) El operador tiene conocimientos técnicos insuficientes y poca experiencia práctica, y debe ser utilizado por personal familiarizado con los durómetros;
(2) Si la carga es demasiado rápida, el tiempo de retención de la carga será corto y las piezas de baja dureza tendrán una dureza alta. Si la carga es demasiado lenta, el tiempo de retención de la carga será prolongado y la dureza será baja. La carga debe ser suave durante la operación y se debe mantener un cierto tiempo de carga. - Factores que afectan las piezas que se prueban.
(1) Los diferentes acabados superficiales muestran diferentes efectos en la prueba de dureza Rockwell. Cuanto menor sea el acabado de la superficie, mayor será la dureza durante la prueba de alta dureza. Por el contrario, cuanto menor sea la dureza, la superficie rugosa con marcas de cuchillo será la primera en enfriarse más rápido durante el enfriamiento, o la superficie muy dura tendrá un valor de dureza alto. Por el contrario, cuando las piezas templadas y revenidas se templan a alta temperatura, la estructura de la superficie con marcas de cuchillo cambiará primero, la capacidad de resistir el templado será pequeña y el valor de dureza será bajo. Al probar piezas con un acabado superficial inferior a 7, es necesario usar una muela abrasiva de desecho para pulir finamente, luego limarlas con una lima o usar una muela abrasiva manual fina para pulirlas y luego limpiarlas.
(2) Hay manchas de sal, arena y otras sustancias en la superficie de las piezas tratadas térmicamente. Cuando se aplica una carga, las piezas se deslizarán. Si hay grasa, la cabeza de diamante actuará como lubricante cuando se presione, reduciendo la fricción y aumentando la profundidad de la indentación. Estas dos razones hacen que el valor de dureza medido sea bajo. El valor de dureza de las piezas probadas donde la capa superficial de óxido es delgada disminuye y el valor de dureza de la parte donde la capa superficial de óxido es densa aumenta. Las piezas cuya dureza se va a medir deben retirarse de la escala y limpiarse sin suciedad.
(3) El error en las pruebas de dureza de superficies inclinadas (o cónicas), superficies esféricas y piezas cilíndricas es mayor que el de las superficies planas. Cuando el penetrador presiona la superficie de dicha pieza, la resistencia alrededor del punto de indentación es menor que la superficie plana e incluso puede desviarse o deslizarse. La profundidad de la indentación aumenta y la dureza disminuye. Cuanto menor sea el radio de curvatura, mayor será la pendiente y más significativa será la reducción del valor de dureza. El penetrador de diamante también se daña fácilmente. Para tales piezas, se debe diseñar un banco de trabajo especial para que el banco de trabajo y el penetrador sean concéntricos. - La influencia del penetrador.
(1) El penetrador de diamante no cumple con los requisitos técnicos o está desgastado después de un período de uso. Si el operador no puede juzgar la calidad del diamante, puede verificarla una agencia de medición y pruebas.
(2) El penetrador de bolas de acero tiene resistencia y dureza insuficientes y es propenso a deformarse. Cuando la bola de acero se aplana y se deforma permanentemente, se convierte en una elipse. Cuando el eje corto es perpendicular a la superficie de la pieza, la sangría es poco profunda y el valor de indicación es alto. Cuando el eje largo es perpendicular a la superficie de la pieza, la sangría se vuelve más profunda y el valor de indicación disminuye. La tolerancia de la bola de acero es tan pequeña como 0,002. mm. - Cargar aspecto.
(1) Carga inicial: Hay fricción entre el resorte y el husillo, la palanca y el comparador, provocando un aumento o disminución de 100N. El tornillo de ajuste está flojo, el bloque de ajuste se mueve y la varilla eyectora está en una posición incorrecta. Hay una diferencia en la línea de salida, provocando que la carga inicial sea incorrecta. Si la carga inicial es incorrecta, se debe ajustar la coordinación de resortes, husillos, palancas, indicadores de cuadrante, etc. Después de que la posición del bloque de ajuste se haya movido adecuadamente, apriete el tornillo de ajuste y la posición de la varilla eyectora al mismo tiempo. La tolerancia de la carga inicial debe ser inferior al 12%.
(2) Carga principal: La relación de palanca es incorrecta, el peso de equilibrio de la pluma y el peso son incorrectos; el eje, la palanca y el peso se desvían, lo que provocará un error en la carga principal. El ratio de apalancamiento es incorrecto y debería ajustarse. Si la hoja está desgastada se debe reparar o reemplazar, y si el eje está deformado se debe enderezar. Se deben corregir las deflexiones del eje, la palanca y el peso. La tolerancia de la carga principal de varias escalas es inferior al 10,5%. - El durómetro no está instalado correctamente.
El probador de dureza no está en posición horizontal y su valor es bajo al probar la dureza. Utilice un nivel de burbuja para medir el nivel y luego nivele el probador de dureza. - La superficie de una determinada parte de prueba está en mal contacto con el banco de trabajo o el punto de apoyo es inestable.
Esto provocará deslizamientos, rodamientos, deformaciones, etc., lo que no sólo hará que los resultados sean inexactos, sino que también dañará el instrumento. Se debe diseñar un banco de trabajo adecuado en función de la geometría de la pieza. - Influencia del entorno circundante.
Los durómetros utilizados en la producción en fábrica a menudo se ven afectados por las vibraciones del entorno, lo que hace que la estructura del instrumento se afloje y el valor de indicación sea inestable. El durómetro debe instalarse en un lugar sin vibraciones o lejos de la fuente de vibración.