El análisis metalográfico es uno de los medios importantes de investigación experimental sobre materiales metálicos. Utilizando principios metalográficos cuantitativos, la morfología espacial tridimensional de la estructura de la aleación se determina midiendo y calculando la microestructura metalográfica de muestras metalográficas bidimensionales o películas delgadas, estableciendo así una relación cuantitativa entre la composición, estructura y propiedades de la aleación. La aplicación de sistemas de procesamiento de imágenes al análisis metalográfico tiene las ventajas de una alta precisión y alta velocidad, lo que puede mejorar en gran medida la eficiencia del trabajo.
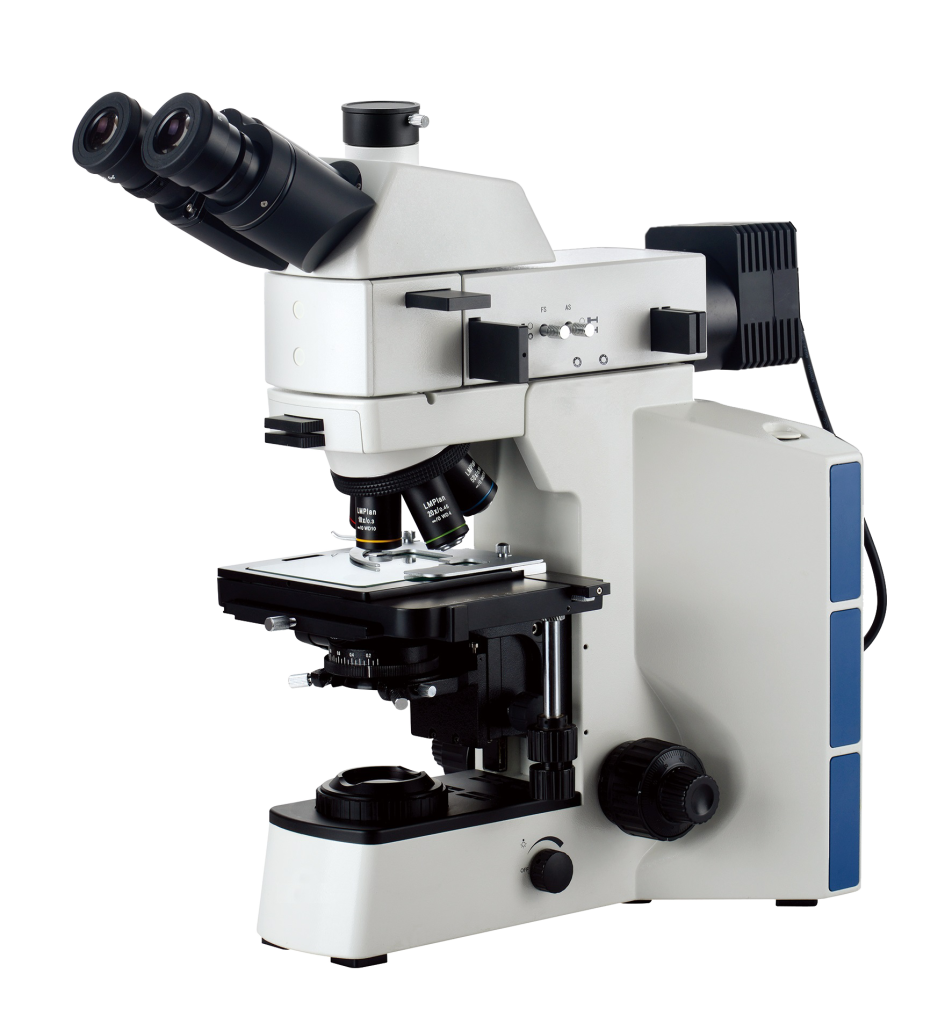
El análisis metalográfico cuantitativo por computadora se está convirtiendo gradualmente en una poderosa herramienta para analizar y estudiar diversos materiales, establecer relaciones cuantitativas entre la microestructura y diversas propiedades de los materiales y estudiar la cinética de la transformación de la estructura del material.
Al utilizar un sistema de análisis de imágenes por computadora, se pueden medir convenientemente varios parámetros, como el porcentaje de área, el tamaño promedio, el espaciado promedio, la relación de aspecto, etc., de los objetos característicos. Con base en estos parámetros, se puede determinar la forma espacial tridimensional, la cantidad, el tamaño y la distribución de los objetos característicos, y se puede establecer una relación interna con el rendimiento mecánico de los materiales, proporcionando datos confiables para una evaluación más científica y un uso racional de los mismos. materiales.
Los principales elementos de prueba incluyen:
- Inspección metalográfica de soldadura;
- Examen metalográfico del hierro fundido;
- Inspección de calidad del tratamiento térmico;
- Inspección y evaluación microscópica de diversos productos metálicos y materias primas;
- Inspección de defectos de bajo aumento en hierro fundido, acero fundido, metales no ferrosos y materias primas;
- Medición de la dureza del metal (HV, HRC, HB, HL) y clasificación del tamaño del grano;
- Determinación del contenido de inclusiones no metálicas;
- Determinación de la profundidad de la capa de descarburación/endurecimiento de la carburación, etc.
Procedimientos de prueba comunes:
Paso 1: Determinar el lugar de selección de la muestra y el método de muestreo
Seleccione el lugar de muestreo y la superficie de inspección, teniendo en cuenta las características y tecnología de procesamiento de la muestra, y el lugar seleccionado debe ser representativo.
Paso 2: Incrustación.
Si el tamaño de la muestra es demasiado pequeño o su forma es irregular, es necesario incrustarla o sujetarla.
Paso 3: Molienda gruesa de la muestra.
El propósito del desbaste es aplanar la muestra y molerla hasta darle una forma adecuada. Los materiales de acero en general a menudo se muelen toscamente con una amoladora, mientras que los materiales más blandos se pueden alisar con una lima.
Paso 4: Molienda fina de la muestra.
El propósito del esmerilado de precisión es eliminar los rayones más profundos que quedan durante el esmerilado basto y prepararlo para el pulido. Para los métodos generales de molienda de materiales, existen dos tipos: molienda manual y molienda mecánica.
Paso 5: Pulido de muestra.
El propósito del pulido es eliminar los finos rayones que quedan al pulir y crear una superficie de espejo brillante y sin marcas. Generalmente se divide en tres tipos: pulido mecánico, pulido químico y pulido electrolítico, siendo el más utilizado el pulido mecánico.
Paso 6: Corrosión de la muestra.
Para observar la microestructura de muestras pulidas bajo un microscopio, se debe realizar corrosión metalográfica. Existen muchos métodos de corrosión, incluida la corrosión química, la corrosión electrolítica y la corrosión de potencial constante, siendo la corrosión química la más utilizada.