Bien que le testeur de dureté Rockwell ait une structure simple et soit facile à utiliser, s’il est mal utilisé pendant une longue période et que le test de dureté est inexact, la qualité du produit sera grandement affectée et entraînera des conséquences néfastes.
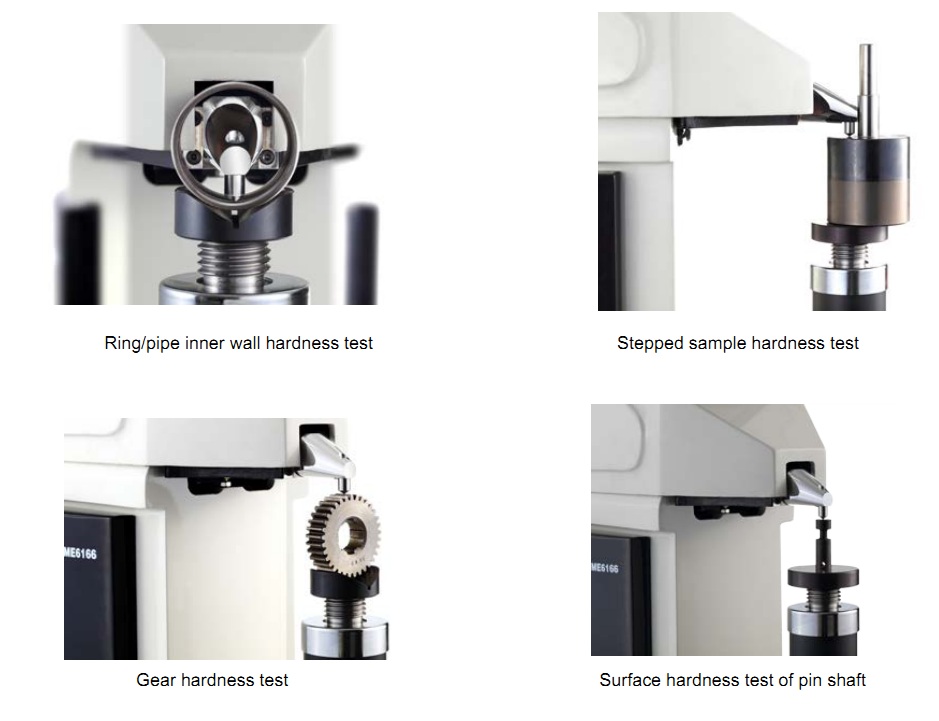
Nous allons maintenant présenter plusieurs erreurs courantes et leurs méthodes de traitement lors de l’étalonnage comme suit :
- Erreur humaine.
(1) L’opérateur a des compétences techniques insuffisantes et une faible expérience pratique, et doit être utilisé par du personnel familiarisé avec les testeurs de dureté ;
(2) Si le chargement est trop rapide, le temps de maintien de la charge sera court et les pièces à faible dureté auront une dureté élevée. Si le chargement est trop lent, le temps de maintien de la charge sera long et la dureté sera faible. Le chargement doit être fluide pendant le fonctionnement et un certain temps de chargement doit être maintenu. - Facteurs affectant les pièces testées.
(1) Différentes finitions de surface montrent différents effets sur le test de dureté Rockwell. Plus l’état de surface est faible, plus la dureté est élevée lors du test de dureté élevée. Au contraire, plus la dureté est faible, la surface rugueuse avec des marques de couteau sera la première à refroidir le plus rapidement lors de la trempe, ou la surface très dure aura une valeur de dureté élevée. Au contraire, lorsque les pièces trempées et revenues sont trempées à haute température, la structure de surface avec les marques de couteau changera en premier, la capacité de résistance au revenu sera faible et la valeur de dureté sera faible. Lors du test de pièces avec une finition de surface inférieure à 7, il est nécessaire d’utiliser une meule usagée pour meuler finement, puis de la limer avec une lime, ou d’utiliser une meule fine à main pour la polir, puis de l’essuyer.
(2) Il y a des taches de sel, de sable et d’autres substances sur la surface des pièces traitées thermiquement. Lorsqu’une charge est appliquée, les pièces glissent. S’il y a de la graisse, la tête diamantée agira comme lubrification lorsqu’elle sera enfoncée, réduisant ainsi la friction et augmentant la profondeur d’indentation. Ces deux raisons rendent la valeur de dureté mesurée faible. La valeur de dureté des pièces testées où la couche de peau d’oxyde est mince diminue, et la valeur de dureté de la pièce où la couche de peau d’oxyde est dense augmente. Les pièces dont la dureté doit être mesurée doivent être retirées de la balance et essuyées sans aucune saleté.
(3) L’erreur dans les tests de dureté des surfaces inclinées (ou coniques), des surfaces sphériques et des pièces cylindriques est plus grande que celle des surfaces planes. Lorsque le pénétrateur appuie sur la surface d’une telle pièce, la résistance autour du point d’indentation est inférieure à celle de la surface plane et peut même dévier ou glisser. La profondeur d’indentation augmente et la dureté diminue. Plus le rayon de courbure est petit, plus la pente est grande et plus la réduction de la valeur de dureté est importante. Le pénétrateur de diamant est également facilement endommagé. Pour de telles pièces, un établi spécial doit être conçu pour rendre l’établi et le pénétrateur concentriques. - L’influence du pénétrateur.
(1) Le pénétrateur diamant ne répond pas aux exigences techniques ou est porté après avoir été utilisé pendant un certain temps. Si l’opérateur ne peut pas juger de la qualité du diamant, celle-ci peut être vérifiée par une agence de mesure et de test.
(2) Le pénétrateur à bille en acier a une résistance et une dureté insuffisantes et est sujet à la déformation. Lorsque la bille d’acier est aplatie et déformée de façon permanente, elle devient une ellipse. Lorsque l’axe court est perpendiculaire à la surface de la pièce, l’indentation est peu profonde et la valeur d’indication est élevée. Lorsque le grand axe est perpendiculaire à la surface de la pièce, l’indentation devient plus profonde et la valeur d’indication diminue. La tolérance de la bille d’acier est aussi petite que 0,002. mm. - Aspect de charge.
(1) Charge initiale : Il y a une friction entre le ressort et la broche, le levier et le comparateur à cadran, provoquant une augmentation ou une diminution de 100N. La vis de réglage est desserrée, le bloc de réglage bouge et la tige d’éjection est dans une mauvaise position. Il y a une différence dans la ligne de départ, ce qui rend la charge initiale incorrecte. Si la charge initiale est incorrecte, la coordination des ressorts, des broches, des leviers, des comparateurs à cadran, etc. doit être ajustée. Une fois que la position du bloc de réglage s’est déplacée de manière appropriée, serrez la vis de réglage et la position de la tige d’éjection en même temps. La tolérance de la charge initiale doit être inférieure à 12 %.
(2) Charge principale : le rapport de levier est incorrect, le poids d’équilibrage de la flèche et le poids sont incorrects ; la broche, le levier et le poids sont déviés, ce qui entraînera une erreur de la charge principale. Le ratio de levier est erroné et devrait être ajusté. Si la lame est usée, elle doit être réparée ou remplacée, et si la broche est déformée, elle doit être redressée. Les déviations de la broche, du levier et du poids doivent être corrigées. La tolérance de la charge principale de différentes échelles est inférieure à 10,5 %. - Le testeur de dureté n’est pas installé correctement.
Le testeur de dureté n’est pas en position horizontale et sa valeur est faible lors du test de dureté. Utilisez un niveau à bulle pour mesurer le niveau, puis nivelez le testeur de dureté. - La surface d’une certaine partie de test de la pièce est en mauvais contact avec l’établi ou le point d’appui est instable.
Cela provoquerait un glissement, un roulement, une déformation, etc., ce qui non seulement rendrait les résultats inexacts, mais endommagerait également l’instrument. Un établi approprié doit être conçu en fonction de la géométrie de la pièce. - Influence du milieu environnant.
Les testeurs de dureté utilisés dans la production en usine sont souvent affectés par les vibrations de l’environnement, ce qui provoque le relâchement de la structure de l’instrument et l’instabilité de la valeur d’indication. Le testeur de dureté doit être installé dans un endroit sans vibration ou loin de la source de vibration.