Metallographic analysis generally involves microscopic observation of cross-sections. Most of the samples after cutting have irregular shapes, making it inconvenient to clamp and grind the samples. Therefore, most of the cut samples need to be mounted into standard-sized shapes.
The metallographic mounting machine fills the resin particles into the mold, heats them to a liquid state, tightly covers the sample after pressurization, and demolds after solidification. Hot mounting is mostly used for solid materials that are heat and pressure resistant. Hot mounting is fast and simple, and the samples are dense and standard, so most metal materials use hot mounting to prepare samples.
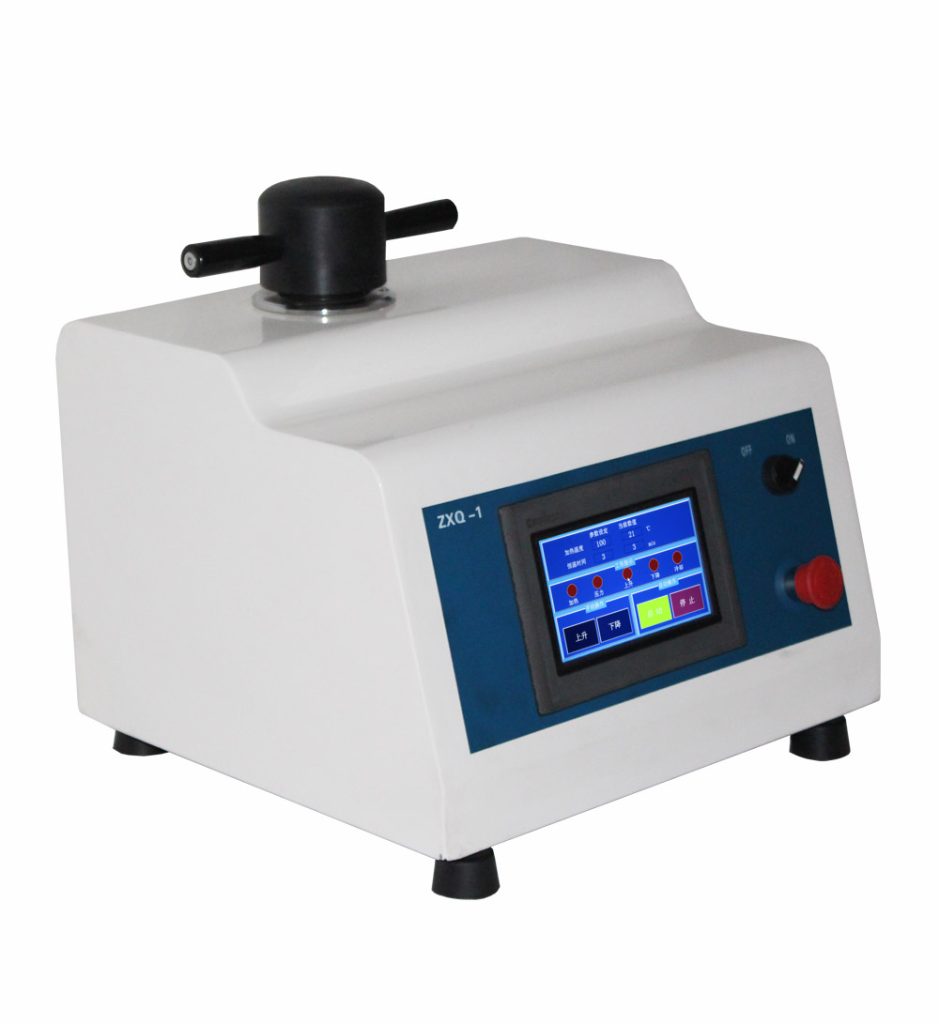
Most of the defects of hot mosaic come from three aspects: incorrect resin selection, insufficient equipment functions, and improper process parameter settings. They are described in detail below:
- Wrong resin selection
During the grinding and polishing process of the mounted sample, it is hoped that the sample part and the mounting material part can be ground simultaneously to obtain a flat observation surface. However, in fact, the grinding rate depends on the material hardness. Inconsistent grinding due to hardness differences often results in inconsistent grinding. This will produce rounded corners at the edges of the sample, making it impossible to focus on the same focal plane and causing observation distortion. Usually, the edge part of the sample is also a very important observation area, which affects the observation effect.
- Insufficient equipment functions
The hot-mounted resin has poor permeability after softening and requires external pressure to achieve densification. Especially for edge-preserving high-hardness resin, it cannot be compressed with a pressure below 20MPa. It is impossible for a hand-cranked thousand-yuan machine to achieve densification. Pressurization is also not enough, and a hydraulic mounting machine with an independent hydraulic station must be used. The following are some mounting defects caused by insufficient pressure.
- Improper parameter setting
Key parameters in the hot mounting process include temperature, holding time, pressure, holding time, cooling rate, etc. The parameter settings required for various resins are different. Acrylic is a typical sensitive sample. If the parameters are not good, it will cause a central fog, and in severe cases, it may even crack.
In addition to obvious visual defects, many mounting defects cannot be discovered until microscopic observation. For example, the interface between the resin and the sample is not well combined, there are tiny gaps, and different suspensions are stored during grinding and polishing, resulting in repeated infections. Completely eliminate scratches, or they may overflow again during observation, forming stains on the surface of the sample and interfering with observation.
All microscopic analysis is the accumulation and crystallization of countless details, and the same is true for metallographic analysis. Even the smallest error may create obstacles for subsequent observations. Industry practitioners must be in awe and pursue perfection.