In the competitive world of motorcycle manufacturing, ensuring the durability and reliability of components is paramount. One crucial aspect of this assurance is the use of fatigue testing machines. These specialized devices play an essential role in evaluating the performance and longevity of motorcycle parts under cyclic loading conditions, ultimately contributing to the safety and satisfaction of riders.
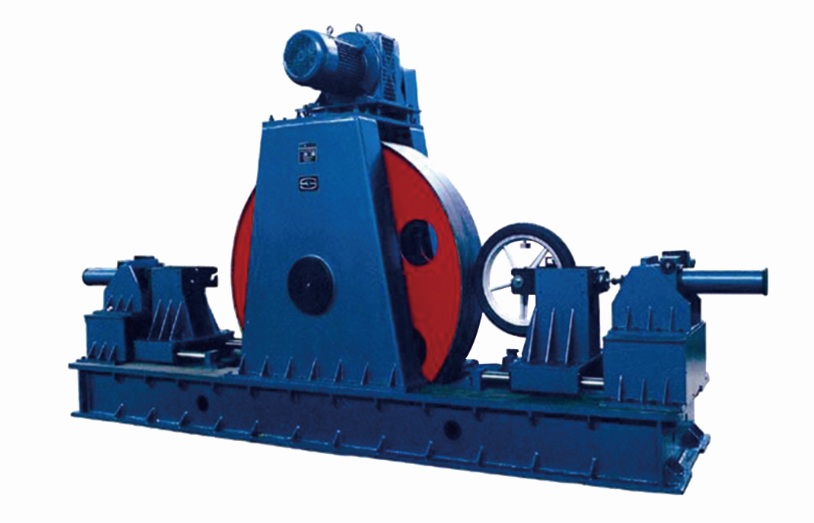
Understanding Fatigue Testing
Fatigue testing is a method used to determine how materials and components behave under repeated stress. In the context of motorcycle manufacturing, this involves subjecting parts such as frames, suspension components, and engine elements to simulated operational conditions over extended periods. The objective is to identify potential failure points and predict the lifespan of these components in real-world scenarios.
The Importance of Fatigue Testing Machines
Fatigue testing machines are designed to apply controlled loads to motorcycle components, replicating the stresses they would encounter during normal use. These machines can simulate various loading conditions, including tension, compression, and torsion. By doing so, manufacturers can gather essential data on how materials respond to fatigue and how long they can withstand repeated stress before failure occurs.
1. Material Selection and Quality Assurance: One of the primary roles of fatigue testing machines is to aid in the selection of materials. By testing different alloys and composites, manufacturers can determine which materials offer the best resistance to fatigue. This information is crucial for ensuring that only the highest quality materials are used in production, ultimately leading to safer and more reliable motorcycles.
2. Design Validation: Fatigue testing is also vital in the design phase of motorcycle components. Engineers can use data from fatigue tests to refine designs, ensuring that parts can withstand the expected loads without failing. This iterative process helps to identify weaknesses early in the design stage, reducing the risk of costly recalls or failures in the field.
3. Compliance with Industry Standards: The motorcycle industry is governed by strict safety and performance standards. Fatigue testing machines help manufacturers comply with these regulations by providing empirical data that demonstrate the durability of their products. Meeting these standards is not only essential for legal compliance but also for maintaining a brand’s reputation in a highly competitive market.
4. Continuous Improvement: The insights gained from fatigue testing are invaluable for continuous improvement in manufacturing processes. By analyzing test results, manufacturers can identify trends and make data-driven decisions to enhance product quality. This commitment to improvement fosters innovation and helps manufacturers stay ahead of the competition.
In summary, fatigue testing machines are an indispensable part of the motorcycle manufacturing process. They provide critical data that informs material selection, validates designs, ensures compliance with industry standards, and drives continuous improvement. As the industry evolves and demands for higher performance and safety increase, the role of fatigue testing will only become more significant. By investing in advanced fatigue testing technologies, motorcycle manufacturers can enhance the reliability of their products, ensuring a safer and more enjoyable riding experience for motorcycle enthusiasts around the world.