Hardness testing is a common method used to determine the strength and durability of materials in various industries. However, one question that often arises is whether hardness testing is destructive or non-destructive.
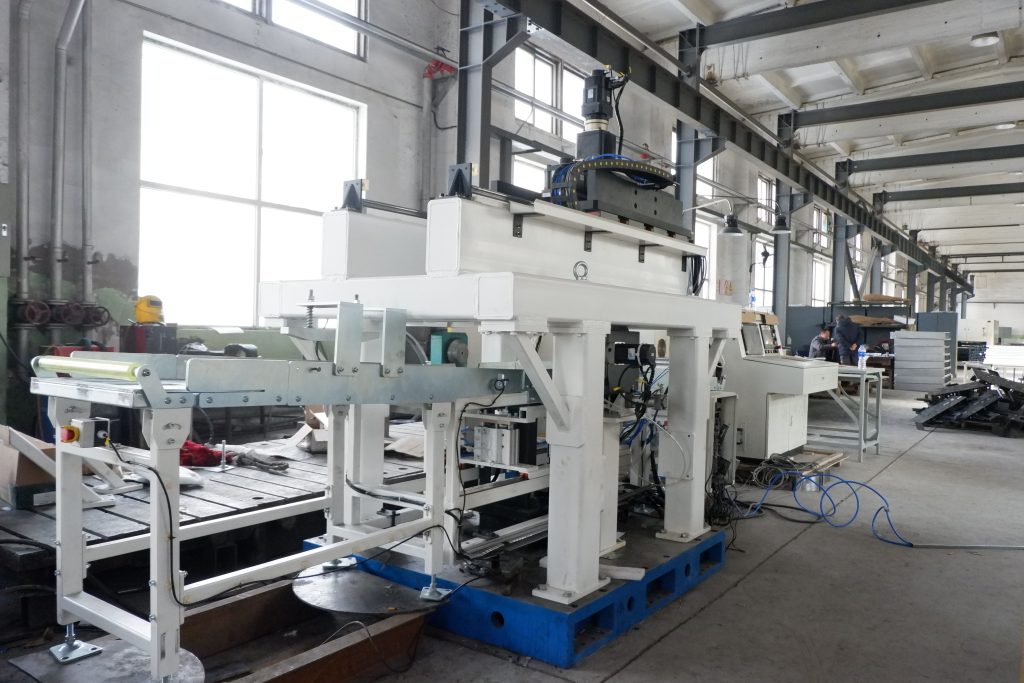
Hardness testing involves applying a specific amount of force to a material’s surface and measuring the depth or size of the indentation left behind. There are different methods of hardness testing, including Rockwell, Brinell, Vickers, and Knoop tests, each with its own advantages and limitations.
While hardness testing provides valuable information about a material’s mechanical properties, it can be considered destructive to some extent. This is because the process of applying force to the material’s surface can cause damage, such as scratching, denting, or deforming the surface.
In some cases, the damage caused by hardness testing may be minimal and not affect the overall integrity of the material. However, in more sensitive applications where surface quality is critical, the damage caused by hardness testing may be unacceptable.
To address this issue, non-destructive methods of hardness testing have been developed, such as ultrasonic and electromagnetic techniques. These methods allow for the evaluation of a material’s hardness without causing any physical damage to the surface.
While traditional hardness testing methods can be considered destructive to some extent, non-destructive alternatives are available for applications where surface integrity is a concern. It is important for industries to carefully consider the potential impact of hardness testing on their materials and choose the most appropriate testing method based on their specific requirements.