In various industries, the application and assessment of paint on non-metal surfaces are critical for ensuring quality and durability. Whether in automotive, aerospace, or furniture manufacturing, understanding the thickness of paint coatings can significantly impact performance, appearance, and longevity. One effective tool for measuring paint thickness on non-metal substrates is the ultrasonic coating thickness gauge. This article explores the principles, applications, and advantages of using ultrasonic technology for paint measurement on non-metal surfaces.
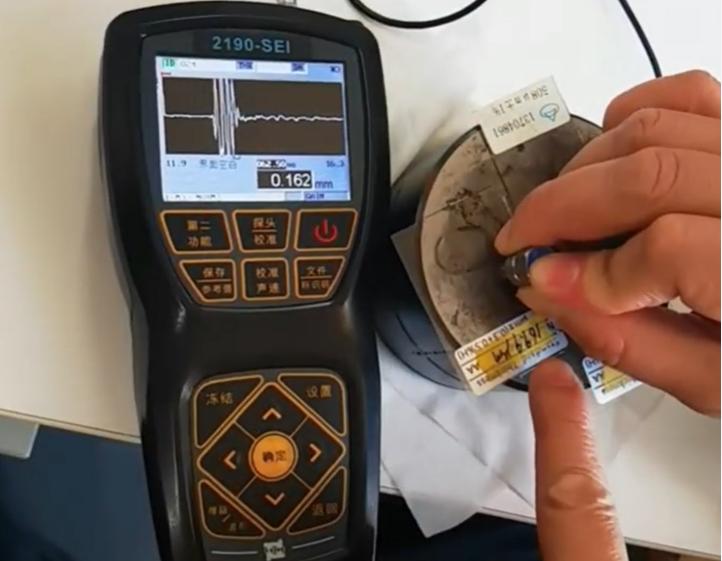
Understanding Ultrasonic Coating Thickness Gauges
Ultrasonic coating thickness gauges operate on the principle of ultrasonic sound waves. These devices emit high-frequency sound waves that travel through the coating material. When the sound waves reach the interface between the coating and the substrate, a portion of the waves is reflected back to the gauge. By measuring the time it takes for the sound waves to return, the gauge can calculate the thickness of the coating based on the speed of sound in the material.
Applications of Ultrasonic Gauges on Non-Metal Surfaces
Ultrasonic coating thickness gauges are particularly useful for measuring paint on non-metal surfaces such as plastics, wood, and composites. These materials are commonly used in various applications, including:
1. Automotive Industry: In automotive manufacturing and repair, ensuring the right paint thickness is essential for aesthetics and protection against corrosion. Ultrasonic gauges can accurately measure paint thickness over plastic and composite body parts.
2. Aerospace: For aircraft components made from composite materials, maintaining the correct paint thickness is crucial for weight management and aerodynamics. Ultrasonic gauges provide precise measurements without damaging the surface.
3. Furniture Manufacturing: In the production of wooden furniture, achieving a uniform paint finish is vital for quality control. Ultrasonic gauges can help manufacturers monitor and maintain the desired thickness of coatings.
4. Electronics: Many electronic devices feature non-metal casings. Accurate paint thickness measurements ensure proper insulation and protection, enhancing the device’s reliability and safety.
Advantages of Ultrasonic Measurement
Using ultrasonic coating thickness gauges for paint measurement on non-metal surfaces offers several advantages:
– Non-Destructive Testing: Ultrasonic gauges do not damage the coating or the substrate, allowing for repeated measurements without affecting the integrity of the material.
– High Accuracy and Precision: These gauges provide accurate readings, which are essential for quality control and compliance with industry standards.
– Versatility: Ultrasonic gauges can be used on a wide range of non-metal materials, making them a versatile tool for various industries.
– Ease of Use: Most ultrasonic gauges are user-friendly, featuring digital displays and simple interfaces that allow operators to take measurements quickly and efficiently.
The measurement of paint thickness on non-metal surfaces is a critical aspect of quality control in multiple industries. Ultrasonic coating thickness gauges offer an effective and reliable solution for assessing coating thickness, ensuring that products meet aesthetic and functional requirements. As technology advances, these gauges continue to improve in accuracy and usability, making them an essential tool for manufacturers and quality assurance professionals alike. By leveraging ultrasonic technology, industries can achieve better results in their coating processes, leading to enhanced product performance and customer satisfaction.