L’analisi metallografica è uno degli strumenti più importanti della ricerca sperimentale sui materiali metallici. Utilizzando principi metallografici quantitativi, la morfologia spaziale tridimensionale della struttura della lega viene determinata misurando e calcolando la microstruttura metallografica di campioni metallografici bidimensionali o film sottili, stabilendo così una relazione quantitativa tra composizione, struttura e proprietà della lega. L’applicazione di sistemi di elaborazione delle immagini all’analisi metallografica presenta i vantaggi di un’elevata precisione e di un’elevata velocità, che possono migliorare notevolmente l’efficienza del lavoro.
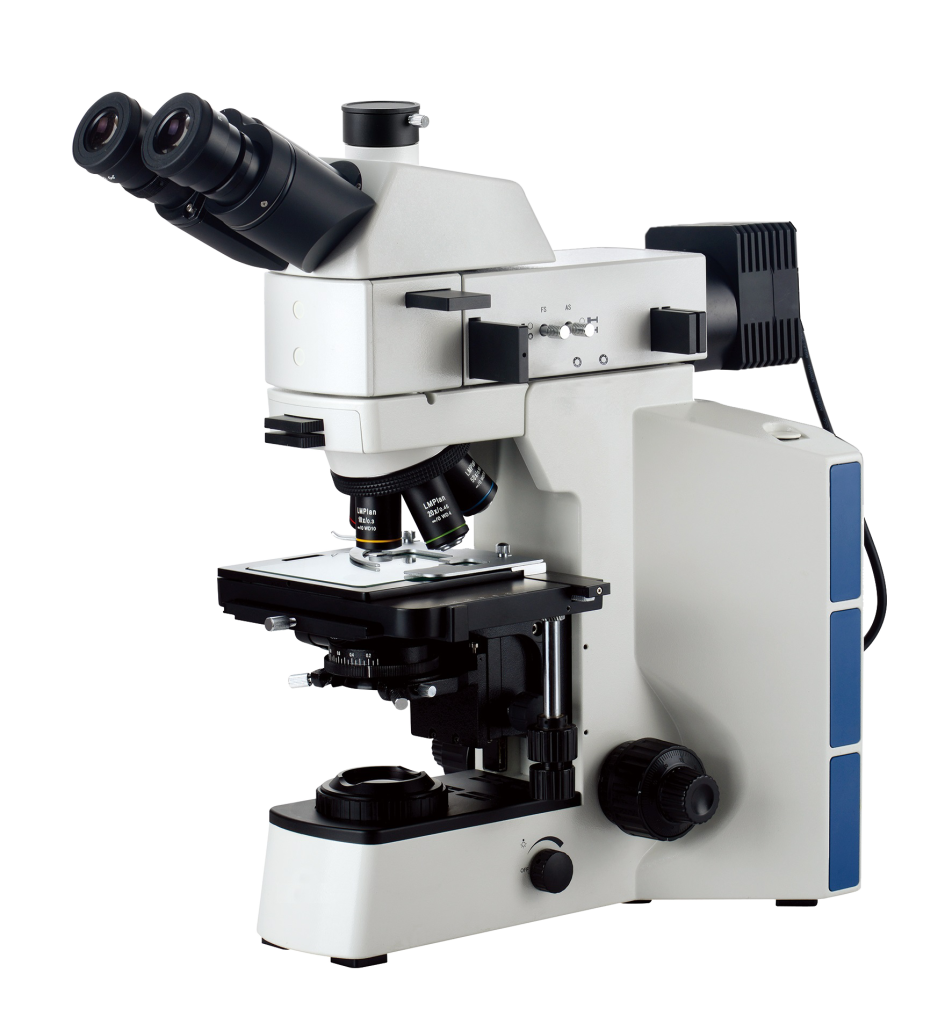
L’analisi metallografica quantitativa computerizzata sta gradualmente diventando un potente strumento per analizzare e studiare vari materiali, stabilire relazioni quantitative tra la microstruttura e le varie proprietà dei materiali e studiare la cinetica della trasformazione della struttura del materiale.
Utilizzando un sistema di analisi delle immagini del computer, è possibile misurare comodamente vari parametri come la percentuale dell’area, la dimensione media, la spaziatura media, le proporzioni, ecc. degli oggetti caratteristici. Sulla base di questi parametri, è possibile determinare la forma spaziale tridimensionale, la quantità, la dimensione e la distribuzione degli oggetti caratteristici e stabilire una relazione interna con le prestazioni meccaniche dei materiali, fornendo dati affidabili per una valutazione più scientifica e un uso razionale dei materiali. materiali.
I principali elementi di test includono:
- Ispezione metallografica delle saldature;
- Esame metallografico della ghisa;
- Controllo di qualità del trattamento termico;
- Ispezione microscopica e valutazione di vari prodotti metallici e materie prime;
- Ispezione di difetti a basso ingrandimento in ghisa, acciaio fuso, metalli non ferrosi e materie prime;
- Misura della durezza del metallo (HV, HRC, HB, HL) e classificazione della dimensione del grano;
- Determinazione del contenuto di inclusioni non metalliche;
- Determinazione della profondità dello strato di decarburazione/indurimento da carburazione, ecc.
Procedure di test comuni:
Passo 1: determinare il luogo di selezione del campione e il metodo di campionamento
Selezionare il luogo di campionamento e la superficie di ispezione, tenendo conto delle caratteristiche e della tecnologia di lavorazione del campione, e il luogo selezionato deve essere rappresentativo.
Passaggio 2: Intarsio.
Se la dimensione del campione è troppo piccola o la sua forma è irregolare, è necessario incorporarlo o fissarlo.
Passaggio 3: macinazione grossolana del campione.
Lo scopo della macinazione grossolana è appiattire il campione e macinarlo in una forma adatta. I materiali generici in acciaio vengono spesso macinati grossolanamente su una smerigliatrice, mentre i materiali più morbidi possono essere levigati con una lima.
Passaggio 4: macinazione fine del campione.
Lo scopo della molatura di precisione è eliminare i graffi più profondi lasciati durante la molatura grossolana e preparare la lucidatura. Per i metodi generali di macinazione dei materiali, esistono due tipi: macinazione manuale e macinazione meccanica.
Passaggio 5: lucidatura del campione.
Lo scopo della lucidatura è rimuovere i graffi sottili lasciati dalla lucidatura e creare una superficie a specchio lucida e senza tracce. È generalmente diviso in tre tipi: lucidatura meccanica, lucidatura chimica e lucidatura elettrolitica, la più comunemente utilizzata è la lucidatura meccanica.
Passaggio 6: Corrosione del campione.
Per osservare la microstruttura dei campioni lucidati al microscopio, è necessario eseguire la corrosione metallografica. Esistono molti metodi di corrosione, tra cui la corrosione chimica, la corrosione elettrolitica e la corrosione a potenziale costante, di cui la corrosione chimica è quella più comunemente utilizzata.