産業メンテナンスに携わる者の最終的な目標は、機械資産の最適な完全な耐用年数を達成することです。これを行うには、現在のメンテナンス プロセスを変更するか、少なくとも多くのプラントの動作方法を変更する必要があります。
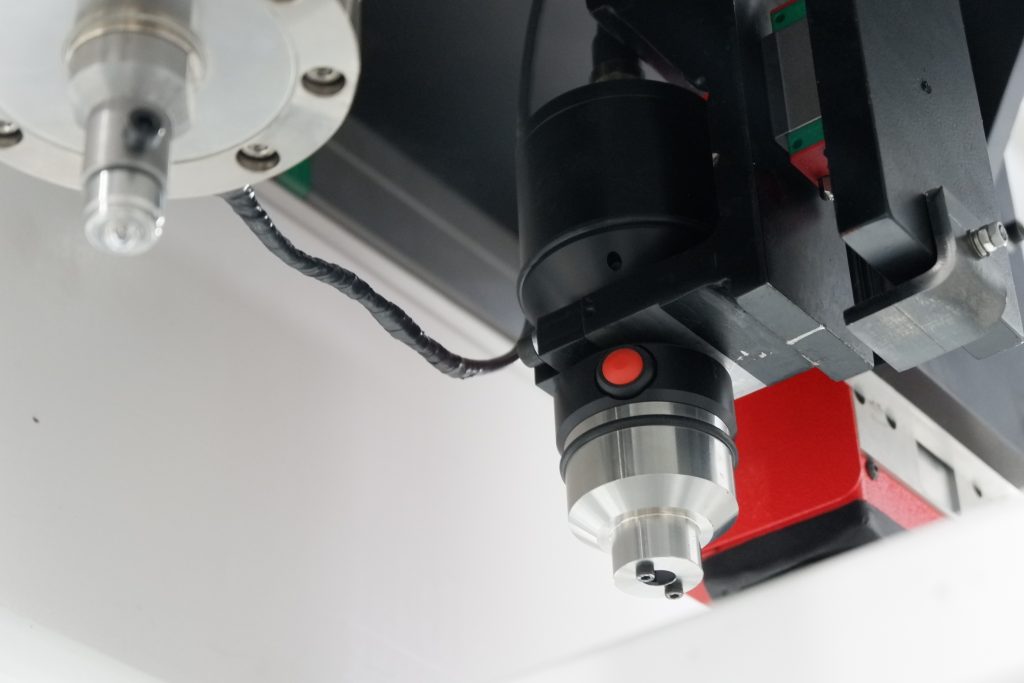
多くの企業は何らかの状態ベースの保守プログラムを導入していますが、なぜ依然として機械の故障が発生するのかについて混乱しています。必要に応じてメンテナンスを行うのは問題ありませんが、だからといってマシンの故障がなくなるわけではありません。まず、状態監視が機能する理由を説明しましょう。
状態ベースのメンテナンスの背後にある前提は、ほとんどの障害は、障害が発生しようとしているという事実について何らかの警告を提供するということです。
PからFまでの間隔
潜在的な障害を測定および検出するためのさまざまな技術が多数あります。あなたにとって最適なマシンをお選びいただけます。たとえば、回転の遅いトランスミッションを使用している場合は、オイル分析を使用できます。潜在的な故障を測定するための一般的な機器は、振動、超音波、オイル分析、温度ですが、他にもたくさんあります。
潜在的な障害が早期に検出されるほど、P-F 間隔は長くなります。 P-F 間隔が長いほど、必要なチェックが少なくなり、さらに重要なことに、障害の結果を回避するために必要なアクションを実行するために必要な時間が長くなります。
このような状態ベースの保守や状態検出は有効ですか?
はい、ダウンタイムを回避でき、コストも節約できる可能性があるためです。
失敗はさまざまな方法で私たちに起こりますが、当然のことながら、私たちはそれと戦うためのさまざまな方法を持っています。潜在的な障害を十分に早期に検出できれば、それを回避できることになります。修理やメンテナンスのためのダウンタイムをスケジュールできます。これは故障ではなく、マシンが停止したり、シャットダウンしたりするものではありません。これはコストの回避であり、工場はダウンタイムコストによる生産の損失を節約します。ダウンタイムを回避し、ダウンタイムを制御し、メンテナンス作業をスケジュールします。これは勝利だ。
二次的トラウマについて考えてみましょう。シールがトランスミッションにある可能性があり、交換にはさらに費用がかかります。引っかからずにベアリングが汚れている場合は、ギアボックスのオーバーホールが必要になります。しかし、ベアリングがシャフトに固着してしまうと、シャフトを交換する必要があり、場合によってはそれ以上の交換が必要になります。
二次被害の代償は莫大になる可能性があるため、状態監視は効果があり、うまく行えば時間と費用を大幅に節約できます。ただし、状態監視には問題があり、予知保全についても同様です。まだ機械の故障が続いています。
根本原因の分析と欠陥の除去は必須
狂気の定義は、同じことを何度も繰り返し、異なる結果を期待することです。故障の原因を特定せずにベアリングを交換し続けるのは気が狂っているのでしょうか?
私たちは原因を見つけずに結果を修正することに苦しんでいませんか?障害/影響を修正するだけが事後保守です。状態ベースの保守プログラムまたはその他のプログラムには、欠陥除去プロセスが必要です。通常、根本原因分析を通じて行われます。これは、問題を定義、理解、解決するプロセスです。
この特性要因図 (下の画像を参照) は、根本原因分析のための基本的なツールです。私たちの時代では、それは故障分析と呼ばれていました。結果はマシンのダウンタイムであることはわかっていますが、障害の本当の原因は何ですか?
このプロセスでは、失敗の理由をブレインストーミングできるように、部門を超えたチームを構築します。これは良い考えですが、検査されるプロセスについて直接知識を持っている人を必ず配置する必要があります。単に部門を代表するだけではありません。その後、段階的なプロセスを経て、失敗の本当の原因を特定します。
ただし、これは私たちが使用するツールの 1 つにすぎず、私のお気に入りの「なぜなぜ」方法も使用しています。問題の根本原因にたどり着くまで、「なぜ」という質問を十分な回数繰り返すだけです。もちろん、質問を 5 つだけに制限する必要はなく、好きなだけ質問することができます。
これらは利用可能なツールのほんの 2 つです。故障モード影響解析 (FMEA) などの他の手法もあります。何を使用するとしても、重要なのは、メンテナンス プロセスの一環として欠陥を排除する必要があるということです。
欠陥をなくすことでその原因が解消され、機械資産の寿命が長くなります。考え方は、「決して修正しないのではなく、常に修正する」ことを保証することです。したがって、何かが故障した場合には、時間の経過とともに故障の数を減らし、稼働時間を増やすために、同じことが再び起こらないようにする必要があります。
オーバーホール、修理、再設計のいずれであっても、欠陥を除去した後は、機械を再設置する必要があります。そのためには精密なメンテナンスのスキルと技術が必要です。
精密なメンテナンス
精度の維持は簡単であり、受け入れられた基準に従って作業することを意味します。あなたとあなたのチームが同意する許容レベル。許容差が狭いほど、結果は良くなります。しかし、計り知れないほどの寛容さを持つことはできません。
精度の維持は「スキルアップ」を意味します。適切なツールを用意するだけでなく、適切なトレーニングも重要です。機械的許容基準、精度バランス、アライメント、ベース平坦度基準、機械応力除去など
機械寿命の支配要因
デザイン
機械の設計は機械の寿命に影響します。ただし、メンテナンスでは、与えられた設計をそのまま受け入れなければならないことがよくあります。これは、用途に対して十分に設計されていないポンプであると仮定します。これは、ポンプが要件を満たしていないため、故障した状態で使用を開始することを意味します。したがって、明らかに、設計が正しくなければ、必然的に再設計が行われます。故障解析では、機械の設計を見直す必要があります。
機械はライフサイクル全体を通じて複数回のオーバーホールを受けます。これを正しく行うことが非常に重要です。多くの企業は設備がないため、この作業を外部委託します。オーバーホール中の最大の問題の 1 つは汚染だからです。機械をオーバーホールする場合、最も重要な点は、機械の適合性に関して OEM 仕様を維持することです。目標は、再び新しく見えるようにすることです。
インストールが重要です。これはあらゆるマシンに関して最も重要なことです。適切に設計された機械や適切にメンテナンスされた機械も、設置が不十分だと台無しになる可能性があります。
デバッグは実際にはインストールの続きです。実際、インストールに関するドキュメントを確認することから始める必要があります。信頼性グループではなく、別のグループが行うべきだと思います。マシンごとに異なるため、リストを公開することはできませんが、すべての OEM 操作手順に従う必要があります。ここでは、ボタンを押して機械を起動したときの熱膨張を測定して、機械を稼働させる前に修正が必要かどうかを確認する必要があります。
Debugging is actually a continuation of installation. In fact, you should start by checking the installation documentation. I think it should be done by another group, not the reliability group. Every machine is different, so we cannot publish a list, but all OEM operating procedures should be followed. This is where you should measure the thermal expansion when the button is pressed to start the machine so we know if any corrections are needed before putting the machine into service.
While the machine is online, different parameters such as temperature, sound and vibration should be measured as part of your condition-based maintenance plan. These measurements are the baseline you will use to compare new measurements taken throughout the life of the machine. Changes in these results mean the machine is degrading. However, if you understand the root cause well and use precision maintenance techniques in the areas you can control, it should be because the machine is wearing out and has a good long life.
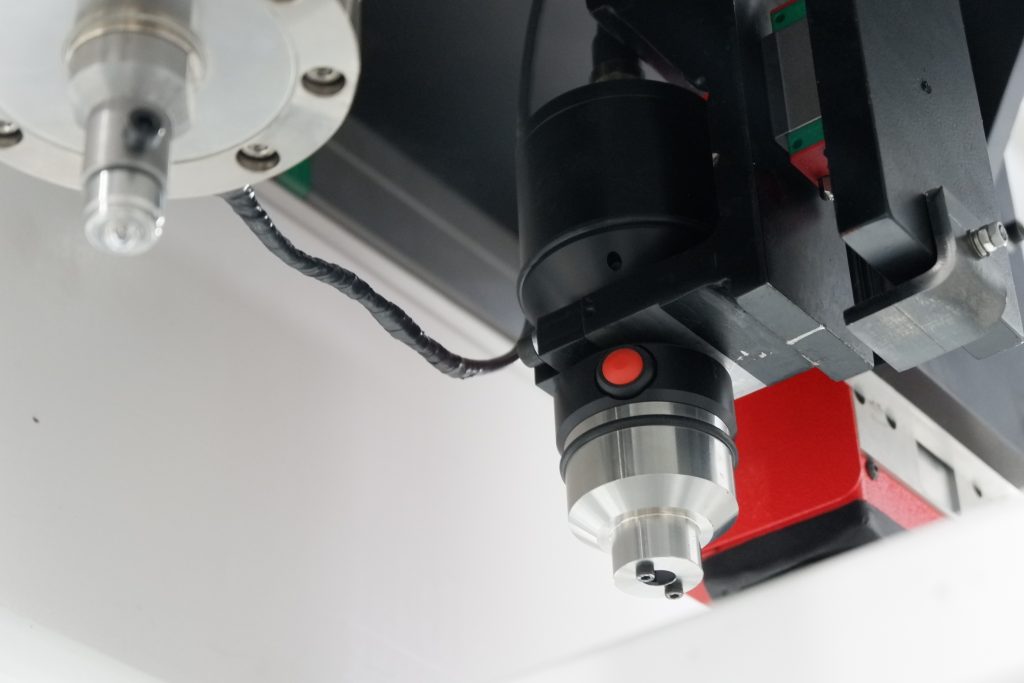
多くの企業は何らかの状態ベースの保守プログラムを導入していますが、なぜ依然として機械の故障が発生するのかについて混乱しています。必要に応じてメンテナンスを行うのは問題ありませんが、だからといってマシンの故障がなくなるわけではありません。まず、状態監視が機能する理由を説明しましょう。
状態ベースのメンテナンスの背後にある前提は、ほとんどの障害は、障害が発生しようとしているという事実について何らかの警告を提供するということです。
PからFまでの間隔
潜在的な障害を測定および検出するためのさまざまな技術が多数あります。あなたにとって最適なマシンをお選びいただけます。たとえば、回転の遅いトランスミッションを使用している場合は、オイル分析を使用できます。潜在的な故障を測定するための一般的な機器は、振動、超音波、オイル分析、温度ですが、他にもたくさんあります。
潜在的な障害が早期に検出されるほど、P-F 間隔は長くなります。 P-F 間隔が長いほど、必要なチェックが少なくなり、さらに重要なことに、障害の結果を回避するために必要なアクションを実行するために必要な時間が長くなります。
このような状態ベースの保守や状態検出は有効ですか?
はい、ダウンタイムを回避でき、コストも節約できる可能性があるためです。
失敗はさまざまな方法で私たちに起こりますが、当然のことながら、私たちはそれと戦うためのさまざまな方法を持っています。潜在的な障害を十分に早期に検出できれば、それを回避できることになります。修理やメンテナンスのためのダウンタイムをスケジュールできます。これは故障ではなく、マシンが停止したり、シャットダウンしたりするものではありません。これはコストの回避であり、工場はダウンタイムコストによる生産の損失を節約します。ダウンタイムを回避し、ダウンタイムを制御し、メンテナンス作業をスケジュールします。これは勝利だ。
二次的トラウマについて考えてみましょう。シールがトランスミッションにある可能性があり、交換にはさらに費用がかかります。引っかからずにベアリングが汚れている場合は、ギアボックスのオーバーホールが必要になります。しかし、ベアリングがシャフトに固着してしまうと、シャフトを交換する必要があり、場合によってはそれ以上の交換が必要になります。
二次被害の代償は莫大になる可能性があるため、状態監視は効果があり、うまく行えば時間と費用を大幅に節約できます。ただし、状態監視には問題があり、予知保全についても同様です。まだ機械の故障が続いています。
根本原因の分析と欠陥の除去は必須
狂気の定義は、同じことを何度も繰り返し、異なる結果を期待することです。故障の原因を特定せずにベアリングを交換し続けるのは気が狂っているのでしょうか?
私たちは原因を見つけずに結果を修正することに苦しんでいませんか?障害/影響を修正するだけが事後保守です。状態ベースの保守プログラムまたはその他のプログラムには、欠陥除去プロセスが必要です。通常、根本原因分析を通じて行われます。これは、問題を定義、理解、解決するプロセスです。
この特性要因図 (下の画像を参照) は、根本原因分析のための基本的なツールです。私たちの時代では、それは故障分析と呼ばれていました。結果はマシンのダウンタイムであることはわかっていますが、障害の本当の原因は何ですか?
このプロセスでは、失敗の理由をブレインストーミングできるように、部門を超えたチームを構築します。これは良い考えですが、検査されるプロセスについて直接知識を持っている人を必ず配置する必要があります。単に部門を代表するだけではありません。その後、段階的なプロセスを経て、失敗の本当の原因を特定します。
ただし、これは私たちが使用するツールの 1 つにすぎず、私のお気に入りの「なぜなぜ」方法も使用しています。問題の根本原因にたどり着くまで、「なぜ」という質問を十分な回数繰り返すだけです。もちろん、質問を 5 つだけに制限する必要はなく、好きなだけ質問することができます。
これらは利用可能なツールのほんの 2 つです。故障モード影響解析 (FMEA) などの他の手法もあります。何を使用するとしても、重要なのは、メンテナンス プロセスの一環として欠陥を排除する必要があるということです。
欠陥をなくすことでその原因が解消され、機械資産の寿命が長くなります。考え方は、「決して修正しないのではなく、常に修正する」ことを保証することです。したがって、何かが故障した場合には、時間の経過とともに故障の数を減らし、稼働時間を増やすために、同じことが再び起こらないようにする必要があります。
オーバーホール、修理、再設計のいずれであっても、欠陥を除去した後は、機械を再設置する必要があります。そのためには精密なメンテナンスのスキルと技術が必要です。
精密なメンテナンス
精度の維持は簡単であり、受け入れられた基準に従って作業することを意味します。あなたとあなたのチームが同意する許容レベル。許容差が狭いほど、結果は良くなります。しかし、計り知れないほどの寛容さを持つことはできません。
精度の維持は「スキルアップ」を意味します。適切なツールを用意するだけでなく、適切なトレーニングも重要です。機械的許容基準、精度バランス、アライメント、ベース平坦度基準、機械応力除去など
機械寿命の支配要因
デザイン
機械の設計は機械の寿命に影響します。ただし、メンテナンスでは、与えられた設計をそのまま受け入れなければならないことがよくあります。これは、用途に対して十分に設計されていないポンプであると仮定します。これは、ポンプが要件を満たしていないため、故障した状態で使用を開始することを意味します。したがって、明らかに、設計が正しくなければ、必然的に再設計が行われます。故障解析では、機械の設計を見直す必要があります。
- 点検・整備
機械はライフサイクル全体を通じて複数回のオーバーホールを受けます。これを正しく行うことが非常に重要です。多くの企業は設備がないため、この作業を外部委託します。オーバーホール中の最大の問題の 1 つは汚染だからです。機械をオーバーホールする場合、最も重要な点は、機械の適合性に関して OEM 仕様を維持することです。目標は、再び新しく見えるようにすることです。
- インストール
インストールが重要です。これはあらゆるマシンに関して最も重要なことです。適切に設計された機械や適切にメンテナンスされた機械も、設置が不十分だと台無しになる可能性があります。
- デバッグ
デバッグは実際にはインストールの続きです。実際、インストールに関するドキュメントを確認することから始める必要があります。信頼性グループではなく、別のグループが行うべきだと思います。マシンごとに異なるため、リストを公開することはできませんが、すべての OEM 操作手順に従う必要があります。ここでは、ボタンを押して機械を起動したときの熱膨張を測定して、機械を稼働させる前に修正が必要かどうかを確認する必要があります。
- 機械がオンラインになっている間、状態ベースの保守計画の一環として、温度、音、振動などのさまざまなパラメータを測定する必要があります。これらの測定値は、マシンの耐用年数全体にわたって取得された新しい測定値を比較するために使用するベースラインです。これらの結果の変化は、マシンが劣化していることを意味します。しかし、根本原因をよく理解し、自分でコントロールできる範囲で精密なメンテナンス技術を使用すれば、機械は磨耗しており、十分に長寿命であるはずです。
Debugging is actually a continuation of installation. In fact, you should start by checking the installation documentation. I think it should be done by another group, not the reliability group. Every machine is different, so we cannot publish a list, but all OEM operating procedures should be followed. This is where you should measure the thermal expansion when the button is pressed to start the machine so we know if any corrections are needed before putting the machine into service.
While the machine is online, different parameters such as temperature, sound and vibration should be measured as part of your condition-based maintenance plan. These measurements are the baseline you will use to compare new measurements taken throughout the life of the machine. Changes in these results mean the machine is degrading. However, if you understand the root cause well and use precision maintenance techniques in the areas you can control, it should be because the machine is wearing out and has a good long life.