The purpose of metallographic grinding and polishing machine polishing is to remove the fine wear marks left by fine grinding on the grinding surface of the metallographic specimen, thereby becoming a smooth and flawless mirror surface.
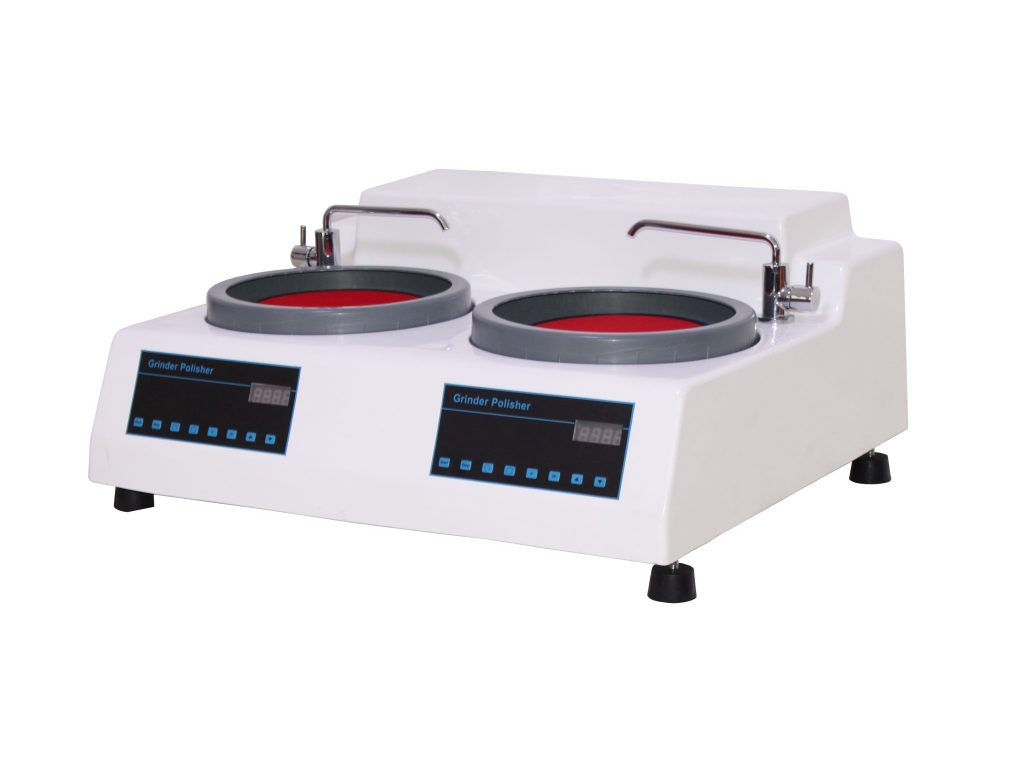
Although polishing is the last process in the preparation of metallographic samples, and thus a smooth mirror surface is obtained, the experience of metallographic workers is: work harder during the polishing process of metallographic samples, because the role of polishing is only can be eliminated.
The surface layer is very thin and has a layer of metal, so polishing performance depends heavily on the quality of the previous process. Sometimes there are some deep wear marks on the grinding surface before polishing, which are difficult to remove even if the polishing time is increased, and usually must be polished again.
Principle of metallographic grinding and polishing mechanical polishing: Mechanical polishing is the result of the relative interaction between the polishing powder and the surface of the metallographic sample. Polishing powder is finer than polishing abrasive. It is generally believed that polishing agents have two effects on the surface of the sample during the polishing process.
The grinding effect of the metallographic grinding and polishing machine: the polishing particles are embedded into the gaps of the polishing fabric to obtain temporary fixation. Its function is similar to polishing sandpaper, but the cuts and scratches produced on the sample surface are much more serious than polishing.
Rolling action of metallographic grinding and polishing machine: Polishing particles are easily released from the polishing fabric and even fly out of the polishing disc. These released particles are sandwiched between the polishing fabric and the grinding surface of the sample during polishing and create a mechanical rolling action on the grinding surface, causing the protrusions on the metal surface to migrate into the recessed parts. In addition the mechanical friction between the polishing fabric and the abrasive surface also contributes to “metal flow”.
Metallographic sample preparation equipment includes metallographic inlay machines, metallographic polishing machines, pre-grinding machines, and metallographic grinding and polishing machines. The metallographic grinding and polishing machine is an all-in-one grinding and polishing machine that can be used for rough grinding. And fine grinding can also be used for polishing.
Maintenance methods of metallographic sample preparation grinding and polishing machine:
- When we use a grinding and polishing machine to grind and polish samples, we must be careful not to use excessive force to avoid damage to the frequency converter or voltage overload.
- In order to make qualified samples, users must remember that it is strictly prohibited to use damaged sandpaper or flannel to grind and polish the samples, so as to avoid accidents.
- After each completion of the grinding and polishing machine work on the sample, remember to clean the grinding and polishing machine. After cleaning, remember to cover the upper cover of the grinding and polishing machine to prevent debris from falling onto the grinding and polishing plate and affecting the test. Sample preparation quality. This not only maintains the grinding and polishing machine well, but also avoids sample quality problems caused by unclean grinding and polishing discs.
- It is recommended that the motor bearing grease of the metallographic sample preparation grinding and polishing machine be replaced once a year.