Thickness testing of FRP tanks is an important part of ensuring their structural integrity, safety and service life, and is widely used in the following scenarios:
Quality control and manufacturing acceptance
- Manufacturing process monitoring: During the production of the tank, the thickness of different parts (such as tank walls, welds, flange connections) is tested to see if they meet the design requirements to avoid insufficient strength due to process defects (such as uneven resin distribution and insufficient fiber layers).
- Factory inspection: Ensure that the thickness of the finished tank is uniform and meets industry standards (such as ASTM, ISO, GB, etc.) to avoid the risk of leakage or rupture caused by thickness deviation.
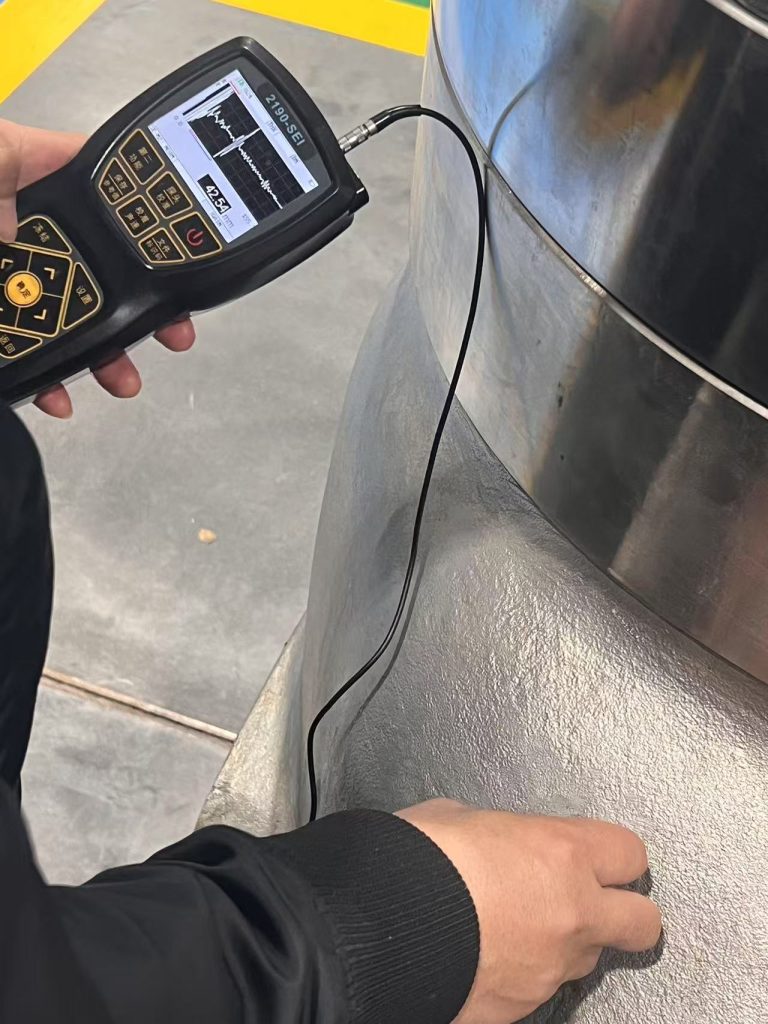
Regular maintenance and safety assessment
- Corrosion and aging monitoring: FRP tanks are exposed to corrosive media such as acids, alkalis, and salts for a long time, which may cause degradation of the resin matrix or peeling of the fiber layer. Regular thickness testing can assess the degree of corrosion and predict the remaining life.
- Mechanical damage inspection: Local structural damage may occur due to collisions and impacts during transportation, installation or use, and weak areas can be found through thickness comparison.
- Pressure vessel compliance inspection: For pressure tanks, thickness is a key parameter for calculating pressure bearing capacity, and regular inspection is required to meet the requirements of regulations such as the “Regulations on Safety Technical Supervision of Pressure Vessels”.
Applications in specific industrial fields
- Chemical and environmental protection industries: Tanks storing hydrochloric acid, sulfuric acid, wastewater and other media need to be frequently inspected to prevent safety accidents or environmental pollution caused by corrosion and leakage.
- Water treatment system: Long-term water pressure of reverse osmosis (RO) tanks and softened water tanks may cause fatigue deformation, and thickness changes need to be monitored.
- Petroleum and energy: Tanks used for oil-water separation or temporary storage of chemicals need to be evaluated for thickness stability in combination with temperature and pressure changes.
- Food and medicine: Ensure that the thickness of the tank lining meets hygiene standards to avoid medium contamination.
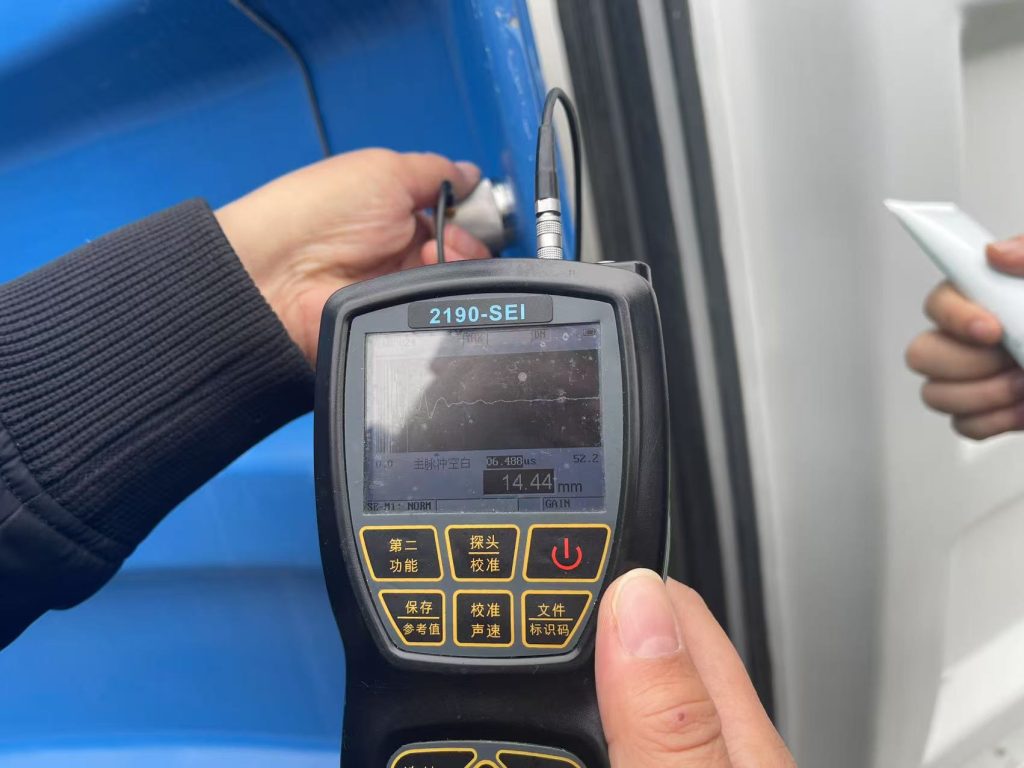
Inspection methods and technologies
- Ultrasonic thickness gauge: The most commonly used method, which measures thickness by sound wave reflection, is suitable for single-layer or multi-layer structures (the material sound velocity needs to be known).
- Electromagnetic induction method: For conductive layers (such as fiberglass tanks with metal linings), non-contact thickness is measured by eddy current effect.
- Mechanical measurement (destructive): Drilling or cutting sampling, high accuracy but will damage the tank body, usually used for laboratory verification.
- Infrared thermal imaging: Indirect detection of temperature differences caused by uneven thickness, suitable for large-area rapid screening.
Significance of detection
- Prevent failure: Insufficient thickness may cause deformation, leakage or even bursting of the tank body, and detection can provide early warning.
- Extend life: Develop maintenance plans (such as reinforcement and coating repair) through data trend analysis.
- Cost control: Avoid high costs of unplanned downtime or sudden replacement.
- Compliance and insurance: Meet safety regulations and reduce corporate liability risks.
Notes
- Standard reference: It is necessary to judge whether the thickness is qualified based on the design drawings or industry standards (such as HG/T 20696-2018 “Glass Fiber Reinforced Plastic Chemical Equipment Design Regulations”).
- Instrument calibration: The equipment needs to be calibrated before testing, considering the impact of temperature and surface curvature on the measurement results.
- Multi-point detection: The top, middle, bottom and pipe joints of the tank need to be measured separately to avoid local deviations.
Through systematic thickness detection, the reliability of FRP tanks can be significantly improved, which is suitable for the full life cycle management from production to scrapping.