Металлографический анализ — один из важных способов экспериментального исследования металлических материалов. Используя количественные металлографические принципы, трехмерную пространственную морфологию структуры сплава определяют путем измерения и расчета металлографической микроструктуры двумерных металлографических образцов или тонких пленок, тем самым устанавливая количественную связь между составом, структурой и свойствами сплава. Применение систем обработки изображений для металлографического анализа имеет такие преимущества, как высокая точность и высокая скорость, что может значительно повысить эффективность работы.
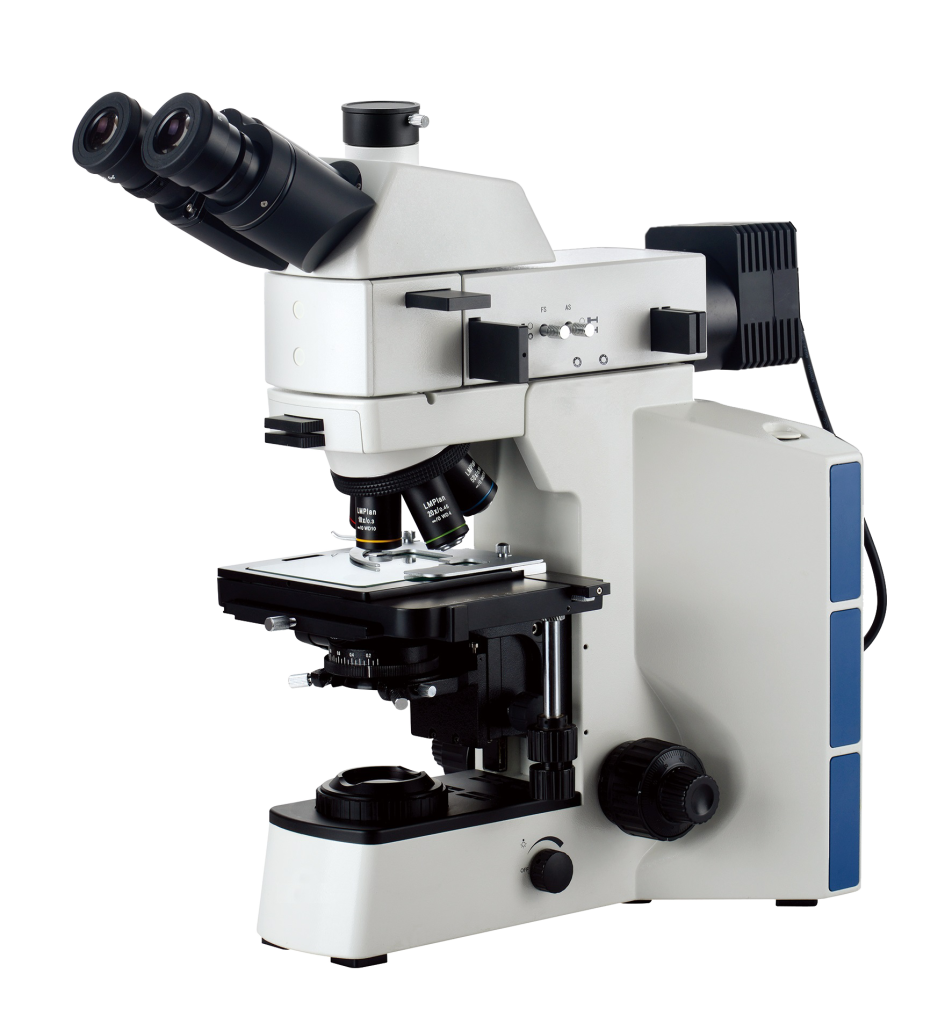
Компьютерный количественный металлографический анализ постепенно становится мощным инструментом анализа и изучения различных материалов, установления количественных связей между микроструктурой и различными свойствами материалов, изучения кинетики трансформации структуры материалов.
С помощью компьютерной системы анализа изображений можно удобно измерить различные параметры, такие как процент площади, средний размер, среднее расстояние, соотношение сторон и т. д. характерных объектов. На основе этих параметров можно определить трехмерную пространственную форму, количество, размер и распределение характерных объектов, а также установить внутреннюю связь с механическими характеристиками материалов, предоставляя надежные данные для более научной оценки и рационального использования материалов. материалы.
Основные элементы тестирования включают в себя:
- Сварочный металлографический контроль;
- Металлографическое исследование чугуна;
- Контроль качества термической обработки;
- Микроскопический контроль и оценка различных металлических изделий и сырья;
- Контроль дефектов малого увеличения в чугуне, литой стали, цветных металлах и сырье;
- Измерение твердости металла (HV, HRC, HB, HL) и сортировка по крупности;
- Определение содержания неметаллических включений;
- Определение глубины обезуглероживающего/науглероженного слоя и т.п.
Общие процедуры тестирования:
Шаг 1: Определите место отбора проб и метод отбора проб
Место отбора проб и поверхность контроля выбирают с учетом характеристик и технологии обработки пробы, при этом выбранное место должно быть репрезентативным.
Шаг 2: Инкрустация.
Если размер образца слишком мал или его форма неправильная, его необходимо заделать или зажать.
Шаг 3: Грубое измельчение образца.
Цель грубого шлифования — сгладить образец и придать ему подходящую форму. Обычные стальные материалы часто грубо шлифуют на шлифовальном станке, а более мягкие материалы можно загладить напильником.
Шаг 4: Тонкое измельчение образца.
Целью прецизионного шлифования является устранение более глубоких царапин, оставшихся при черновой шлифовке, и подготовка к полировке. Для общих методов измельчения материалов существует два типа: ручное шлифование и механическое шлифование.
Шаг 5: Образец полировки.
Цель полировки — удалить мелкие царапины, оставшиеся в результате полировки, и создать блестящую зеркальную поверхность без следов. Обычно ее разделяют на три типа: механическая полировка, химическая полировка и электролитическая полировка, причем наиболее часто используемой является механическая полировка.
Шаг 6: Коррозия образца.
Для наблюдения микроструктуры полированных образцов под микроскопом необходимо провести металлографическую коррозию. Существует множество методов коррозии, включая химическую коррозию, электролитическую коррозию и коррозию при постоянном потенциале, причем наиболее часто используется химическая коррозия.