Fatigue testing machines play a crucial role in the field of material science and engineering. They are designed to evaluate the durability and reliability of materials and components under cyclic loading conditions. Understanding the working principle of a fatigue testing machine is essential for engineers and researchers who aim to assess material performance and predict failure under repetitive stress.
What is a Fatigue Testing Machine?
A fatigue testing machine is a specialized device that applies repeated or fluctuating loads to a specimen over an extended period. The primary objective is to determine the material’s endurance limit, which is the maximum stress level that a material can withstand for an infinite number of cycles without failing. Fatigue testing is vital for industries such as aerospace, automotive, and construction, where material failure can have catastrophic consequences.
Working Principle
The working principle of a fatigue testing machine can be broken down into several key components and processes:
1. Specimen Preparation
Before testing, a specimen is prepared according to standardized dimensions and surface finishes. The specimen is typically made from the material that needs to be tested, such as metals, polymers, or composites.
2. Load Application
The machine applies a controlled cyclic load to the specimen. This can be achieved through various methods, including:
– Axial Loading: Applying tension and compression along the specimen’s length.
– Bending: Subjecting the specimen to a bending moment, creating tension on one side and compression on the other.
– Torsion: Twisting the specimen to create shear stress.
The load can be applied in a sinusoidal, triangular, or random waveform, depending on the testing requirements.
3. Monitoring and Data Acquisition
As the test progresses, the fatigue testing machine continuously monitors the load, displacement, and other relevant parameters. Advanced data acquisition systems collect this information in real-time, allowing for detailed analysis and assessment of the material’s behavior under cyclic loading.
4. Failure Detection
The machine is equipped with sensors to detect when the specimen fails, which can occur in various ways, such as crack initiation or complete fracture. The point of failure is critical data, as it helps determine the material’s fatigue life.
5. Analysis and Reporting
After the test concludes, the data collected is analyzed to establish the material’s fatigue properties. This includes calculating the number of cycles to failure, the stress amplitude, and the endurance limit. The results are typically presented in the form of S-N curves (stress-number of cycles), which graphically represent the relationship between stress levels and the number of cycles to failure.
The fatigue testing machine is an indispensable tool for evaluating the durability of materials under cyclic loads. By understanding its working principle, engineers can better predict material performance, improve design processes, and ultimately enhance safety and reliability in various applications. As technology advances, fatigue testing machines are becoming increasingly sophisticated, incorporating automation and advanced data analysis capabilities to provide even more accurate and efficient testing solutions.
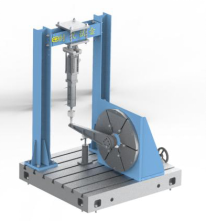