Hardness is the ability of a material to resist hard objects pressing into its surface. Durometer An instrument for measuring the hardness of materials. Depending on the material being measured, hardness testers can be used in different fields. Some hardness testers are widely used in the machining industry. They mainly measure the hardness of metallic materials.
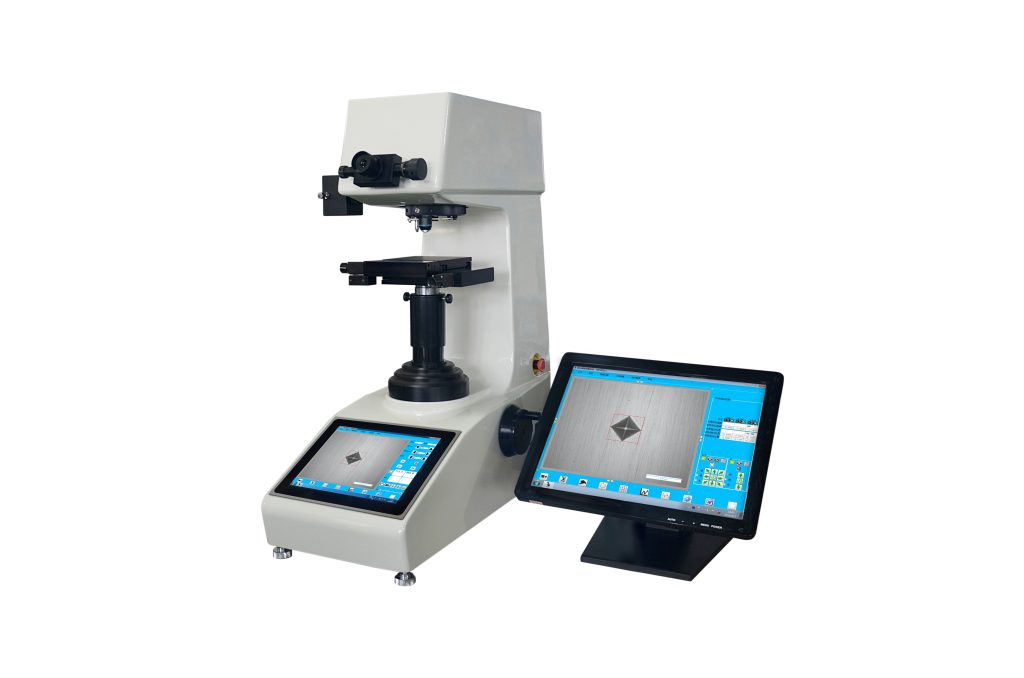
Such as: Vickers hardness tester, Rockwell hardness tester, Brinell hardness tester, Leeb hardness tester, Webster hardness tester, microhardness tester, Shore hardness tester, etc. We usually use the hardness system as relative hardness, then, What issues should we focus on when using a hardness tester?
When using a hardness tester, you should focus on the following issues:
1. The hardness tester itself will produce two kinds of errors: one is the error caused by the deformation and movement of its parts; the other is the error caused by the hardness parameters exceeding the prescribed standards. For the second type of error, the hardness tester needs to be calibrated with a standard block before measurement. For the hardness tester calibration results, the difference is qualified within ±1. A stable value with a difference within ±2 can give a correction value. When the difference is outside the range of ±2, the hardness meter must be calibrated and repaired or other hardness testing methods must be used. Each hardness scale has a practical application range and must be selected correctly according to regulations. Because when it exceeds its specified testing range, the accuracy and sensitivity of the hardness tester are poor, the hardness value is inaccurate, and it should not be used. Hardness testing methods also stipulate corresponding calibration standards. The standard block used to calibrate the hardness tester cannot be used on both sides, because the hardness of the standard side and the back side are not necessarily the same. It is generally stipulated that the standard block is valid within one year from the date of calibration.
2. If the test piece allows, generally select at least three hardness values from different parts to test, take the average, and take the average as the hardness value of the test piece.
3. For specimens with complex shapes, cushion blocks of corresponding shapes should be used and fixed before testing. Round specimens are generally placed in a V-shaped groove for testing.
4. Before loading, check whether the loading handle is in the unloading position. When loading, the movement should be gentle and steady, and do not use too much force. After loading, the loading handle should be placed in the unloading position to prevent the instrument from being under load for a long time and causing plastic deformation, which will affect the measurement accuracy.
5. When replacing the indenter or anvil, be sure to wipe the contact parts clean. After replacement, use a steel sample of a certain hardness to test several times until the hardness values obtained are the same twice in a row. The purpose is to press the contact part between the indenter or anvil and the testing machine tightly and ensure good contact, so as not to affect the accuracy of the test results.