Metallographic analysis is one of the important means of experimental research on metal materials. Using quantitative metallographic principles, the three-dimensional spatial morphology of alloy structure is determined by measuring and calculating the metallographic microstructure of two-dimensional metallographic specimens or thin films, thereby establishing a quantitative relationship between alloy composition, structure, and properties. Applying image processing systems to metallographic analysis has the advantages of high accuracy and fast speed, which can greatly improve work efficiency.
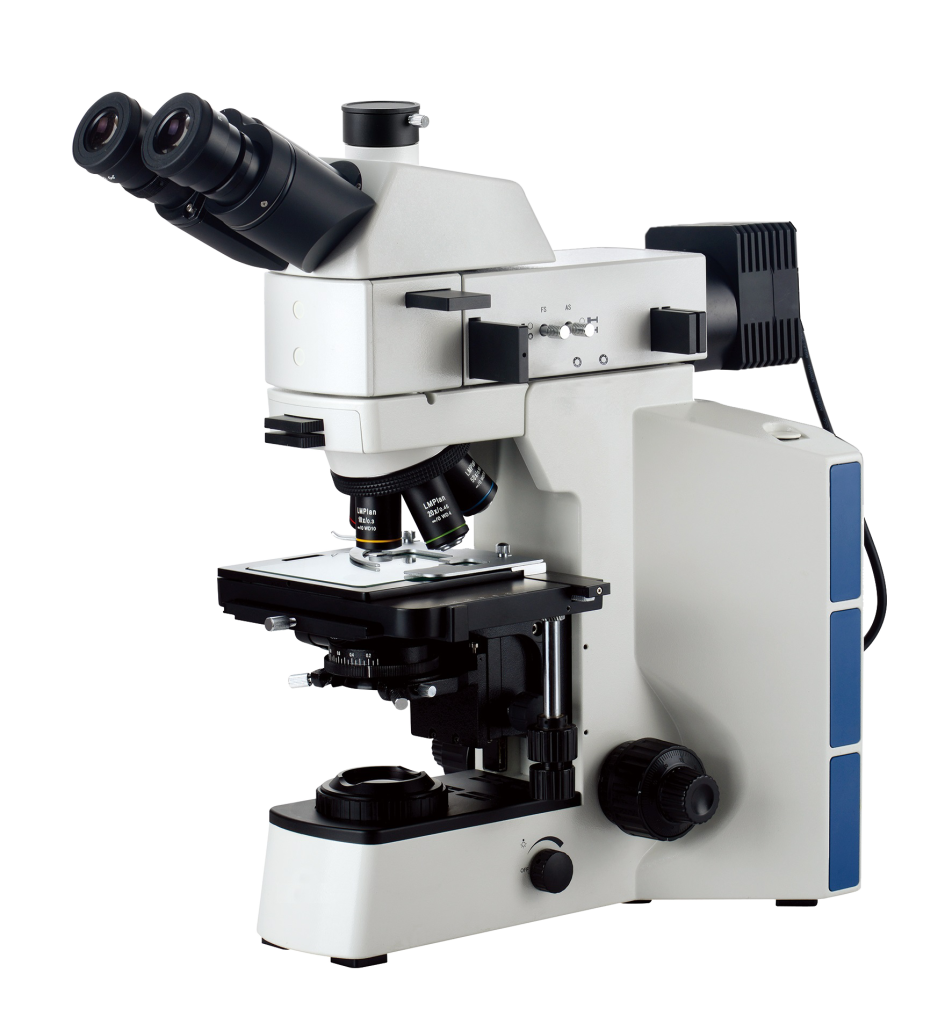
Computer quantitative metallographic analysis is gradually becoming a powerful tool for analyzing and studying various materials, establishing quantitative relationships between the microstructure and various properties of materials, and studying the kinetics of material structure transformation.
By using a computer image analysis system, various parameters such as area percentage, average size, average spacing, aspect ratio, etc. of feature objects can be conveniently measured. Based on these parameters, the three-dimensional spatial shape, quantity, size, and distribution of feature objects can be determined, and an internal relationship can be established with the mechanical performance of materials, providing reliable data for more scientific evaluation and rational use of materials.
The main testing items include:
- Welding metallographic inspection;
- Metallographic examination of cast iron;
- Quality inspection of heat treatment;
- Microscopic inspection and evaluation of various metal products and raw materials;
- Inspection of low magnification defects in cast iron, cast steel, non-ferrous metals, and raw materials;
- Measurement of metal hardness (HV, HRC, HB, HL) and grading of grain size;
- Determination of non-metallic inclusion content;
- Determination of depth of decarburization/carburization hardening layer, etc.
Common testing procedures:
Step 1: Determine the location of sample selection and the method of sampling
Select the sampling location and inspection surface, taking into account the characteristics and processing technology of the sample, and the selected location must be representative.
Step 2: Inlay.
If the size of the sample is too small or its shape is irregular, it needs to be embedded or clamped.
Step 3: Rough grinding of the sample.
The purpose of rough grinding is to flatten the sample and grind it into a suitable shape. General steel materials are often roughly ground on a grinder, while softer materials can be smoothed with a file.
Step 4: Fine grinding of the sample.
The purpose of precision grinding is to eliminate deeper scratches left during rough grinding and prepare for polishing. For general material grinding methods, there are two types: manual grinding and mechanical grinding.
Step 5: Sample polishing.
The purpose of polishing is to remove the fine scratches left by polishing and create a shiny and traceless mirror surface. It is generally divided into three types: mechanical polishing, chemical polishing, and electrolytic polishing, with the most commonly used being mechanical polishing.
Step 6: Corrosion of the sample.
To observe the microstructure of polished samples under a microscope, metallographic corrosion must be performed. There are many methods of corrosion, including chemical corrosion, electrolytic corrosion, and constant potential corrosion, with chemical corrosion being the most commonly used.