Metallographic inspection is an indispensable and important means to control and evaluate product quality. It is an important method for researching materials, new processes and improving the intrinsic quality of materials in scientific research.
The mechanical properties of the sample to be inspected are not only related to its chemical composition, but also closely related to its metallographic structure.
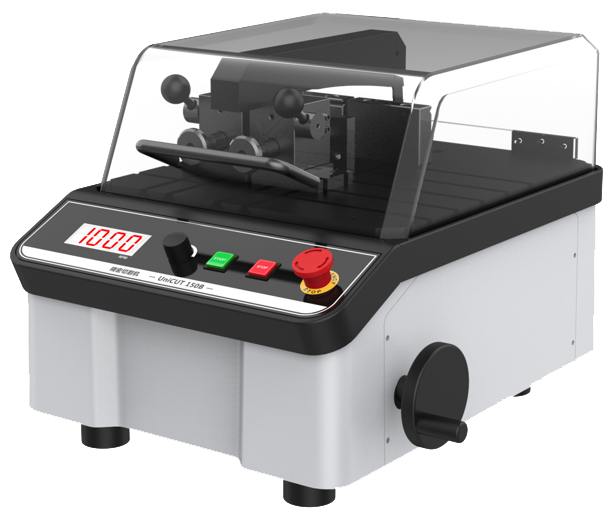
To conduct metallographic analysis, it is necessary to prepare samples that can be used for microscopic examination – metallographic specimens. Usually, the preparation of metallographic specimens goes through several steps of sampling, mounting, grinding and polishing.
Each step should be performed carefully, as physical objects at any stage may affect the final result, as this may create organizational artifacts and lead to erroneous conclusions. The preparation of metallographic samples is completed by cutting machines, mounting machines, and grinding/polishing machines.
The interception of metallographic samples is an important step in the preparation process of metallographic samples. Methods for cutting out patterns include hand saws, sawing machines, grinding wheel cutting machines, wire cutting machines, etc.
Depending on the shape and material of the part, choose the appropriate method for cutting. Grinding wheel cutting machines are mainly widely used in cutting metallographic samples because of their strong adaptability and relatively high cutting accuracy. Resin grinding wheels can cut soft metal parts such as copper, aluminum and alloys and hard metal parts such as quenched Then carbon steel, high speed steel. Diamond cutting blades can cut super-hard materials such as carbide.
Metallographic analysis methods have been applied in the analysis of many types of solid materials including metals, ceramics, plastics, circuit boards, ores, etc., and are also widely used in quality inspection, failure analysis and solid materials research laboratories.