Many people use cutting discs during laboratory testing, because samples need to go through a series of steps such as cutting and sampling before they can be observed more intuitively. However, there are cutting discs and grinding wheel discs on the market, and some users It’s unclear what the difference is. What is the difference between cutting discs and grinding wheel discs? Here is a brief introduction for you.
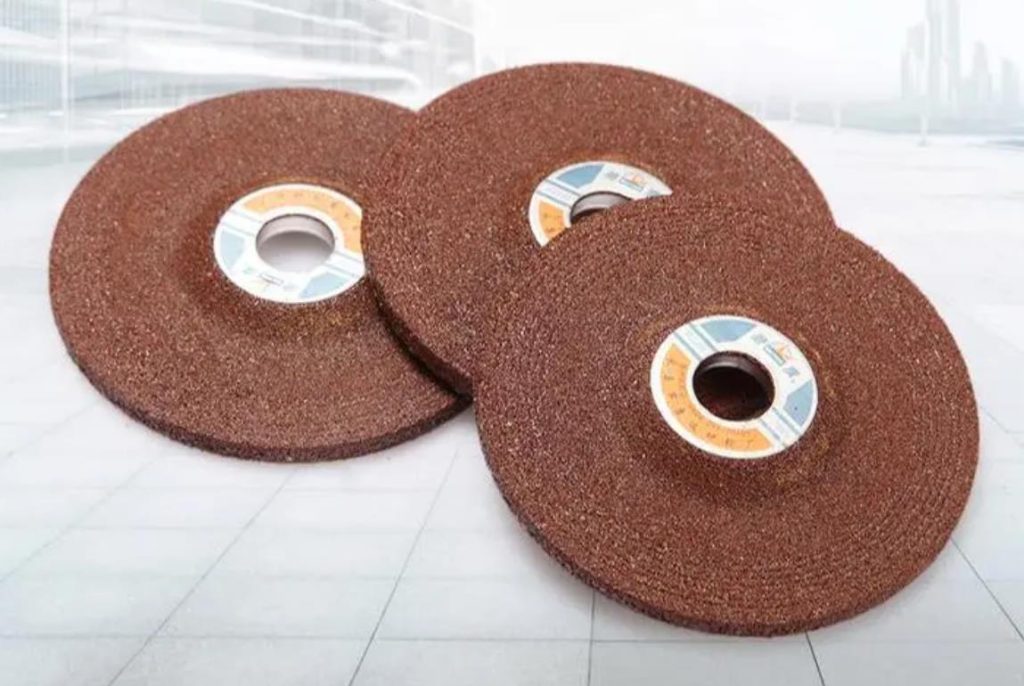
- Their functions are different
The grinding wheel is an abrasive tool for grinding.
Cutting discs are thin sheets used to cut metal.
- They are made differently
Grinding wheel discs are made by adding a bonding agent to the abrasive, compacting, drying and roasting.
The cutting blade is mainly made of glass fiber and resin as reinforced bonding material, which has the characteristics of high tensile strength, impact resistance and bending strength.
According to the abrasives, grinding wheels can be divided into ordinary abrasive (corundum, silicon carbide, etc.) grinding wheels, natural abrasive superabrasives and (diamond, cubic grinding wheels, boron nitride, etc.) grinding wheels;
According to the shape, grinding wheels can be divided into flat grinding wheels, cup grinding wheels, cylindrical grinding wheels, bevel grinding wheels, disc grinding wheels, etc.;
According to the binder, grinding wheels can be divided into metal grinding wheels, rubber grinding wheels, resin grinding wheels, ceramic grinding wheels, etc.
Cutting piece:
According to the material, cutting blades are mainly divided into fiber resin cutting blades and diamond cutting blades.
The former uses resin as a binding agent and combines fiberglass mesh with a variety of materials. It can cut hard materials such as alloy steel and stainless steel. The performance is very significant, and the cutting accuracy is stable, which can greatly improve the cutting efficiency. Save production costs. Its cutting methods include dry and wet.
Diamond cutting blades are mainly used for cutting hard and brittle materials such as stone, new and old roads, prefabricated panels, concrete, and ceramics. It mainly consists of two parts: the base body and the cutter head. The matrix is the main supporting part of the bonded cutter head. The cutter head mainly plays a cutting role because the cutter head contains diamond. As the hardest substance at present, diamond can effectively cut the object to be processed. The cutter head will be worn during use, but the base body will not.
Check before starting:
1) Check whether each fastener is loose, and if so, repair it and tighten it.
2) Focus on checking whether the grinding wheel has cracks. If so, replace it immediately. Inspection method: tap the grinding wheel lightly with a wooden stick until it makes a crisp sound before use.
3) Turn the grinding wheel by hand, observe whether the grinding wheel rotates flexibly and briskly, and listen carefully for any scraping sounds.
4) Check whether the rotation direction of the grinding wheel is correct. The correct direction is when the grinding chips fly downward and away from the grinding wheel.
5) Start the power supply. If the vibration and noise are abnormal and obvious, stop the machine immediately and tag it out for maintenance workers to check.
6) Check that the gap between the outer circle of the grinding wheel and the workpiece bracket should be ≤3mm.
7) Check whether the grounding of the grinder is intact.
Operating requirements:
1) Operators must wear safety glasses and anti-splash masks.
2) The body must be kept at an appropriate distance from the grinding tool.
3) Turn on the power and start grinding only when the grinding wheel runs smoothly.
4) It is strictly forbidden to violently impact the workpiece with the grinding wheel. During grinding, pressure should be gradually applied to protect the grinding wheel from impact force and prevent the grinding wheel from bursting.
5) The distance between the working end and the hand-held end should be kept more than 20 mm.
6) The amount of grinding should be appropriate during each grinding to prevent accidents caused by the workpiece running with the grinding wheel.
7) When grinding for a long time, cold water should be available next to the grinder to prevent the workpiece from getting hot and causing burns during grinding.
8) Steel parts with strong crumbliness cannot be ground on the grinding wheel to prevent the workpiece from breaking.
9) Do not grind the workpiece perpendicular to the diameter of the grinding wheel, that is, do not grind the workpiece on the side of the grinding wheel.
10) The length of the workpiece to be ground should be less than 500 mm. When workpieces longer than 500 mm need to be ground, other grinding tools should be used, such as angle grinders.
11) For a grinding machine in use, the difference in the wear amount of the two grinding wheels between their diameters shall not exceed 20%.
12) After each work is completed, the power supply should be cut off immediately.